Kapitel 8 Kommunikationsschnittstellen
8.1 Allgemeines
Der erste Schritt in der industriellen Kommunikation war die Parallelverdrahtung, bei der alle Teilnehmer einzeln mit der Regel- und Steuerebene verdrahtet wurden. Doch mit steigendem Automatisierungsgrad stieg auch die Anzahl der Teilnehmer, was zu einem hohen Verkabelungsaufwand führte. Mittlerweile wurde die Parallelverdrahtung von den kostengünstigeren und schnelleren Feldbus-Systemen und den Ethernet-basierten Kommunikationsnetzwerken weitgehend abgelöst. Die in den 1980er Jahren entstandenen Feldbus Systeme sind heutzutage nicht mehr aus der Industrie wegzudenken. Als fester Bestandteil komplexer Maschinen und Anlagen werden sie vorrangig in der Fertigungsautomatisierung eingesetzt. Doch auch in der Prozess- oder Gebäudeautomatisierung sowie der Automotive-Technik findet der Feldbus Anwendung. Mithilfe des leitungsgebundenen und seriellen Feldbusses werden Sensoren und Aktoren (die so genannten „Feldgeräte“), wie Motoren, Schalter, Antriebe oder Lampen mit speicherprogrammierbaren Steuerungen (SPS) und Leit- bzw. Prozessrechnern verbunden. Der Feldbus unterstützt folglich den raschen Datenaustausch zwischen den einzelnen Systemkomponenten auch über grosse Distanzen. Die Übertragung der Informationen findet dabei über einen gemeinsamen Bus statt, wodurch entsprechende Protokolle notwendig werden, die regeln welcher Teilnehmer welche Daten zu welchem Zeitpunkt übertragen darf. Selbst starke äussere Belastungen können dem robusten digitalen Signalübertragungssystem nichts anhaben. Da der Feldbus nur über ein Kabel kommuniziert, konnte der Verkabelungsaufwand im Vergleich zur Parallelverdrahtung deutlich gesenkt werden. Ein Feldbus funktioniert typischerweise im so genannten Master-Slave-Betrieb. Während der Master für die Steuerung der Prozesse zuständig ist, arbeiten die Slave-Stationen die einzelnen Teilaufgaben ab. Die Feldbusse werden in der Norm IEC 61158 (Digital data communication for measurement and control) standardisiert. Der vereinfachte Aufbau eines Feldbussystems ist in Abbildung 8.1 dargestellt.
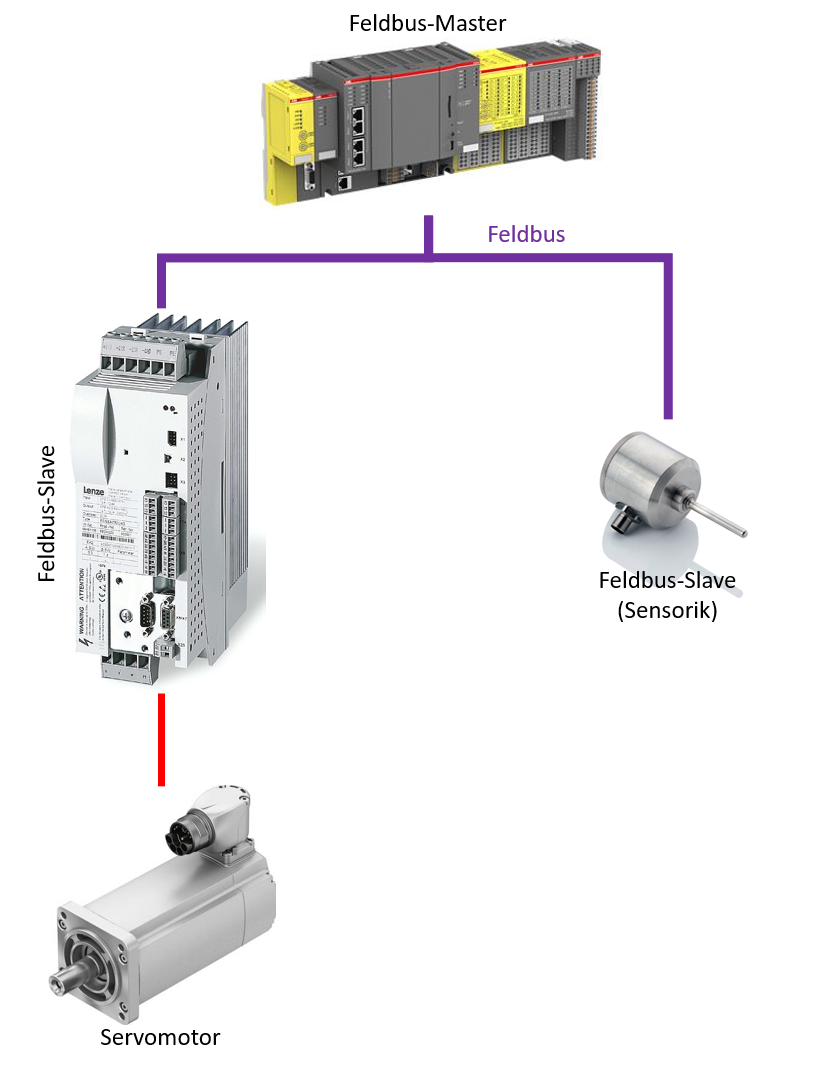
Abbildung 8.1: Vereinfachter Aufbau eines Feldbussystems
Die Aufgabe des Feldbus-Masters besteht darin, die Kommunikation über den Feldbus zu koordinieren. Die Slaves hingegen, bestehend aus Sensoren und Aktoren (z.B. Servoumrichtern), reagieren auf Anfragen des Feldbus-Masters und führen dessen Befehle aus.
Die Vorteile eines Feldbusses sind:
- geringerer Verkabelungsaufwand spart Zeit bei Planung und Installation
- Kabel, Rangierverteiler und Ausmaße des Schaltschranks werden reduziert
- Eigendiagnose durch das System möglich
- Höhere Zuverlässigkeit und bessere Verfügbarkeit durch kurze Signalwege
- Gerade bei analogen Werten erhöht sich der Schutz vor Störungen.
- Offene Feldbusse vereinheitlichen herstellerübergreifend Datenübertragung und Geräteanschluss. - Komponenten verschiedener Hersteller sind zumindest hinsichtlich der Basiskommunikation leichter austauschbar.
- Erweiterungen oder Änderungen sind einfach durchzuführen und garantieren Flexibilität und somit Zukunftssicherheit.
- Die Festlegung von Messbereichen bei Messumformern ist nicht erforderlich. Die (visuelle) Anzeigeskala im Leitsystem kann jederzeit geändert werden.
Die Nachteile eines Feldbusses sind:
- komplexeres System – qualifiziertere Mitarbeiter notwendig
- höherer Preis von Komponenten mit Feldbusfunktionalität
- aufwendige Messgeräte
- etwas längere Reaktionszeit
- Die kleinste tauschbare Einheit wird teurer.
- Durch die Vielzahl verschiedener Feldbusse sind Sensor-/Aktor-Hersteller gezwungen, mehrere - Feldbusse zu unterstützen, was zusätzliche Kosten verursacht. Außerdem ist die Vorhersage, welche Feldbusse in Zukunft an Bedeutung gewinnen bzw. verlieren werden, sehr schwierig. Dadurch besteht die Gefahr von Fehlinvestitionen bei der Entwicklung von Feldbusankopplungen.
- Durch das zentrale Anbindungsprinzip kann bei einer Busstörung das Leitsystem von allen Sensoren und Aktoren abgeschnitten sein. Daher sind eventuell redundante Bussysteme erforderlich.
Die am weitesten verbreiteten Feldbus-Protokolle sind unter anderen:
- Profibus (DP & PA) bzw. ProfiNet (Robotor, Maschinen- und Anlagenbau, Prozessautomation)
- DeviceNet (CAN basierendes, höheres Protokoll)
- Interbus-S (Maschinen- und Anlagenbau)
- SERCOS Interface (Motion Control, CNC, Roboter, Maschinen- und Anlagenbau)
- EtherNet/IP
- Foundation Fieldbus
- Modbus
8.2 Real-Time-Kommunikation
Die Übertragung von Real-Time-Daten bei Feldbussystemen basiert auf dem zyklischen Datenaustausch mit einem Provider-Consumer-Modell. Die Real-Time-Kommunikation unterteilt sich in zwei Gruppen, in RT und in IRT welche entsprechend den Anforderungen eingesetzt werden.
Die RT (Real-Time) Gruppe zeichnet sich dadurch aus, dass eine synchrone Übertragung mit einer Reaktionszeit von ca. 1-100ms stattfindet. Entsprechende Echtzeitprotokolle sind (unter anderen):
- CAN (open)
- Profibus-DP
- Modbus
Die IRT (Isochronous-Real-Time) hingegen zeichnet sich durch eine synchrone Übertragung mit typischen Reaktionszeiten von weniger als 1 Mikrosekunde bei sehr geringem Jitter aus. Beispiele dafür sind:
- SERCOS II von Bosch Rexroth (optisch)
- SERCOS III
- Profinet IRT von Siemens
- EtherCAT von Beckhoff
- Powerlink von B&R (elektrisch)
Die Notwendigkeit für sehr geringe Reaktionszeiten ergibt sich aus der entsprechenden Anwendung. Sehr hohe Ansprüche ergeben sich beispielsweise bei Druckmaschinen. Bei Bahngeschwindigkeiten von mehr als 1000m/min und Reaktionszeiten von 1ms ergeben sich beispielsweise Positionsfehler von mehreren Millimetern. Für Druckmaschinen sind solche Abweichungen unbrauchbar, da die Druckfarben in diesem Fall statt übereinander um mehrere Millimeter versetzt zueinander zum Liegen kommen würden. Es wäre falsch in diesem Zusammenhang die eigentliche Kommunikationsgeschwindigkeit mit der Datenrate zu verwechseln. Die Zeitspanne, die im üngünstigsten Fall vergeht, bis ein Datensatz von der Steuerung bis in den Antrieb übertragen wurde ist somit eine wichtige Kenngrösse für entsprechende Echtzeitsysteme. Diese Zeitspannen treten aus regelungstechnischer Sicht als Totzeiten auf, welche eine destabilisierende Wirkung haben und somit so gering wie möglich ausfallen sollten. Eine Einteilung in entsprechende Echtzeitklassen erfolgt in Abbildung 8.2.
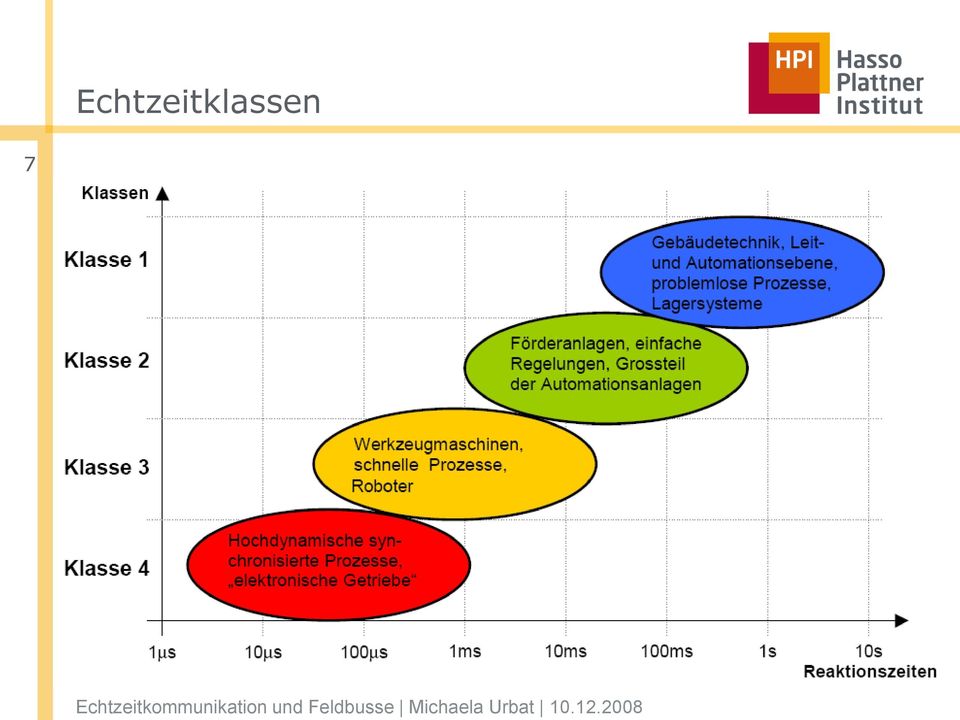
Abbildung 8.2: VKlassifizierung von Echtzeitanwendungen (Quelle: https://docplayer.org/10703539-Echtzeitkommunikation-und-feldbusse.html)
Da momentan viele unterschiedliche Feldbusse auf dem Markt konkurrieren, bieten Hersteller von Antrieben meist entsprechende Kommunikationsadapter als steckbare, optionale Module an.
8.3 SERCOS Protokoll
SERCOS (Serial Real-time Communication System) wurde 1995 als internationale Norm (IEC 61491) und 1998 als europäische Norm (EN 61491) für Antriebe an Industriemaschinen anerkannt. Die digitale Antriebsschnittstelle SERCOS -Interface hat sich seit Beginn der 90er Jahre zu einem weltweit akzeptierten Echtzeit-Kommunikationsstandard für anspruchsvolle Motion-ControlAnwendungen entwickelt. Ihre Attraktivität basiert auf den technischen Eigenschaften – insbesondere Echtzeit, Performance und Störsicherheit – in Kombination mit einem sehr grossen Produkt- und Anbieterspektrum. Folgende Eigenschaften lassen sich den einzelnen SERCOS Protokollen zuordnen:
Eigenschaft | SERCOS I | SERCOS II | SERCOS III |
---|---|---|---|
Einführung | 1987 | 1999 | 2005 |
Physikalisches Medium | Lichtwellenleiter | Lichtwellenleiter | Ethernet |
Netzwerktopologie | Ring | Ring | Ring oder Linie |
Übertragungs-Geschwindigkeit | 2/4 Mbit/s | 2/4/8/16 Mbit/s | 100 Mbit/s |
Jitter | <1us | <1us | <1us |
Anzahl Master | 1 pro Ring | 1 pro Ring | 1 pro Ring/Linie |
Max. Teilnehmer | 254 pro Ring | 254 pro Ring | 511 pro Ring/Linie |
8.4 Profibus Protokoll
Profibus existiert in drei Varianten:
- Profibus DP (Dezentrale Peripherie)
- Profibus PA (Prozess-Automation)
- Profibus FMS (Fieldbus Message Specification)
Profibus DP dient zur Ansteuerung von Sensoren und Aktoren durch eine zentrale Steuerung in der Fertigungstechnik, wobei viele Standarddiagnosemöglichkeiten im Vordergrund stehen. Weitere Einsatzgebiete sind die Verbindung von „verteilter Intelligenz“, also die Vernetzung von mehreren Steuerungen untereinander. Es sind Datenraten bis zu 12 Mbit/s auf verdrillten Zweidrahtleitungen oder Lichtwellenleiter möglich. Der Einsatz mit Antriebsgeräten ist im Profil PROFIdrive festgelegt. Profibus PA wird üblicherweise zur Kommunikation zwischen Mess- und Prozessgeräten, Aktoren und Prozessleitsystem bzw. SPS/DCS in der Prozess- und Verfahrenstechnik eingesetzt. Profibus PA ist eine Profibus-Variante mit für die Prozessautomation geeignetem Physical Layer (Übertragungsschicht), bei welcher an Profibus DP über sogenannte Koppler mehrere Segmente (PA-Segmente) mit Feldgeräten angeschlossen werden können. Die zweiadrige Busleitung dieser Segmente übernimmt nicht nur die Kommunikation, sondern auch die Energieversorgung der Teilnehmer (MBP Übertragungstechnik). Profibus PA stellt eine digitale Alternative zur klassischen analogen Verbindung von Geräten (4- bis 20-mA-Technik) dar und bietet zusätzliche Funktionen durch die bidirektionale Kommunikation. Profibus PA ist durch Leistungsbegrenzung auch für explosionsgefährdete Bereiche geeignet. Je nach Einsatzbereich kommen unterschiedliche Explosionsschutzarten zum Einsatz. Besonders etabliert ist die Schutzart Eigensicherheit. Sie erlaubt einen Zugang zum Feldgerät im laufenden Betrieb ohne einen Heißarbeitserlaubnisschein (FISCO-Spezifikation). Die Datenübertragungsrate von Profibus PA liegt bei 31,25 kbit/s, was für eine hohe Immunität gegen elektromagnetische Interferenzen sorgt und lange Kabelwege ermöglicht. Diese Geschwindigkeit ist für verfahrenstechnische Applikationen völlig ausreichend. Eine weitere Besonderheit von Profibus PA ist das weit verbreitete Geräteprofil „PA Devices“ (PA-Profil), in welchem die wichtigsten Funktionen der Feldgeräte herstellerübergreifend standardisiert sind, was für den Anwender von erheblichem Nutzen ist. Profibus FMS war vor allem für den Einsatz in komplexen Maschinen und Anlagen gedacht, wurde allerdings von DP abgelöst und ist heute nicht mehr Bestandteil der Internationalen Feldbusnorm.
8.5 Achs zu Achs Kommunikation
Sollte die Anwendung des Servonatriebes es notwendig machen mehrere Achsen miteinander zu vernetzen, gibt es die Möglichkeit Daten und Parameter untereinander auszutauschen. In diesem Fall spricht man von Master-Slave-Anwendungen, bei denen ein Antrieb als Master und weitere als Slaves bezeichnet werden. Ein Beispiel für eine solche Anwendung stellt beispielsweise der Winkelsynchronlauf dar, welche häufig auch als elektrisches Getriebe bzw. elektrische Welle bezeichnet wird. In diesem Fall wird die aktuelle Position des Masters synchronisiert an den Slave übertragen. In diesem Falle kommen, in Abhängigkeit von der Datenübertragungsrate CAN- oder serielle Schnittstellen in Frage.
8.6 Schlussbemerkung
Feldbussysteme sind heute fester Bestandteil jeder komplexen Maschine oder Anlage. Die auf www.feldbusse.de vorgestellten Feldbusse werden insbesondere in der Fertigungsautomatisierung eingesetzt. Darüber hinaus gibt es eine Vielzahl weiterer Systeme, die sich aufgrund ihrer technischen Eigenschaften für andere Bereiche der Automatisierung, wie zum Beispiel für die Prozess- oder Gebäudeautomatisierung, eignen und dort ihren Haupteinsatzbereich gefunden haben. In der Praxis ist zu beobachten, dass die Auswahl eines Feldbussystems in den seltensten Fällen nach technischen Kriterien erfolgt. Vielmehr bestimmt in der Regel der Typ der eingesetzten speicherprogrammierbaren Steuerung (SPS), welcher Feldbus zum Einsatz kommt. Der Hauptgrund ist darin zu suchen, dass jeder der führenden SPS-Hersteller eine bestimmte Feldbustechnologie favorisiert. Diese favorisierte Technologie ist optimal in das Programmier- und Konfigurationstool eingebunden und der SPS-Hersteller macht es den Anwendern besonders einfach, mit diesem Feldbus zu arbeiten. Dem Interesse der Hersteller nach Alleinstellungsmerkmalen (Performance, Tool-Integration, etc.) steht der Wunsch der Betreiber nach Austauschbarkeit (Kompatibilität, Kosten etc.) gegenüber. Das führte dazu, dass die anfänglich proprietären Feldbusse heute massgeblich durch firmenübergreifende Interessengruppen weiter entwickelt werden. Die daraus resultierende breitere Produktvielfalt, grössere Konkurrenz und bessere Interoperabilität steigern zusätzlich die Qualität und den erzielbaren Nutzen. Bei den heute massgeblichen Ethernet-basierten Feldbussen führt der Wunsch nach Wahlfreiheit zu Feldbusgeräten, die mehrere Protokolle unterstützen. Die Gerätetechnik wird vereinheitlicht und vereinfacht und das Rennen um die bessere Funktionalität setzt sich mit der Software weiter fort.