Unidad 7 DMAIC4. Mejorar
7.1 Introducción
En esta unidad trabajaremos sobre los siguientes objetivos de aprendizaje:
- Descubrir las actividades a realizar en la etapa Mejorar de un proyecto Lean Seis Sigma.
- Conocer diversas herramientas para la búsqueda de alternativas de mejora.
- Definir en qué consiste un plan de mejora y caracterizar todos los elementos a integrar en él.
7.2 Objetivos
Los objetivos en la etapa MEJORAR del DMAIC son:
- Determinar las estrategias de mejora en un proceso no óptimo.
- Identificar y evaluar mejoras a partir de diversas técnicas basadas en alternativas de cambio.
- Encontrar propuestas de mejora a partir el diseño de experimentos.
- Analizar las propuestas en función de un análisis coste-beneficio.
- Elaborar el plan de mejora con la mejor alternativa elegida.
Una estrategia de mejora es, en pocas palabras, un enfoque sistemático para actuar sobre las X’s determinantes del proceso y seleccionar la mejor forma de llegar a una solución que mejore su funcionamiento. En esta fase es esencial tener en cuenta la naturaleza de las causas raíz que se han confirmado en la fase de analizar. En muchos procesos, especialmente en los transaccionales, para actuar sobre las causas confirmadas no hay una solución única, sino la combinación de varias alternativas. Si un proceso funciona mal porque no tiene instrucciones o métodos de trabajo definidos, formalizar estos métodos no será suficiente para asegurar su funcionamiento. En otros procesos, sobre todo los de fabricación, las causas raíz suelen estar asociadas a factores parámetros de regulación y funcionamiento. Para actuar sobre dichas causas basta con modificar dichos factores “regulándolos” para conseguir el resultado deseado. La estrategia de mejora dependerá pues de la naturaleza de las causas o variables (X’s) determinantes de su actual funcionamiento. En esta sección vamos a tratar sobre las alternativas de cambio al proceso actual, dejando para más adelante las mejoras que suponen actuar sobre los factores de funcionamiento del proceso.
En las fases de Medir y Analizar, se habrán identificado algunas causas de variación y, en algunos casos, se habrán podido confirmar a partir de los datos existentes. Otras veces, para confirmar dichas causas, será necesario realizar pruebas haciendo funcionar el proceso en condiciones tales que permitan esta confirmación, pruebas que son ya mejoras en sí mismas. Tareas, que consumen tiempo pero no aportan nada nuevo al proceso, tales como redundancias, supervisiones no necesarias, lazos de retrabajo, tareas que quedan en “espera” debido al flujo del proceso, tareas que se realizan de modo “artesanal” sin una sistemática de trabajo, tareas que no están siendo medidas y, por tanto, continúan adelante aunque ya lleven implícito el “defecto.” Los anteriores son algunos ejemplos de causas relacionadas con alternativas de cambio al proceso actual.
7.3 Generar soluciones de cambio
Cuando las causas son alternativas de cambio al proceso actual, habitualmente no tenemos posibilidad de utilizar datos históricos (no existen) por lo que debemos generar las posibles soluciones o cambios que, generalmente, no son únicas, y previo estudio de las dificultades o riesgos que puede suponer su aplicación, realizar alguna prueba piloto que permita evaluar su eficacia. Las soluciones más sencillas y eficaces serán las que se apliquen para mejorar el proceso.
Las principales herramientas para generar soluciones de cambio están estrechamente relacionadas con el sistema Lean. Trabajaremos sobre las siguientes:
- Mejorar el flujo del proceso.
- Estandarizar las actividades.
- Pensamiento creativo.
- Benchmarking
- Work-out
- Evaluación del riesgo.
- Análisis de Modo de Fallo y Efecto (AMFE).
- Pruebas piloto.
- Simulación.
- Ventana esfuerzo-beneficio.
- Técnicas 5S.
7.4 Mejorar el flujo
La mejora del flujo del proceso estribará básicamente en las siguientes acciones que podamos llevar a cabo:
- Eliminar o reducir tareas que no añaden valor
- Aproximar tareas relacionadas y físicamente separadas
- Agrupar tareas repartidas en distintos departamentos
- Equilibrar las actividades
7.4.1 Eliminar o reducir tareas que no añaden valor
Un primer grupo de cambios, que seguramente habremos identificado antes, al estudiar el proceso y al medir sus actividades, se centra en modificar el flujo actual del proceso para hacerlo más eficaz y/o eficiente. Entre estos cambios podemos citar la reducción o eliminación de tareas que no añaden valor para el cliente o que no contribuyen a dotar al resultado del proceso de ninguna de sus Y’s. Las burocracias internas, las normas de funcionamiento, a veces rígidas, originan tareas que no siempre son realmente necesarias para asegurar el buen funcionamiento del proceso. Otras veces son los cambios tecnológicos que evitan realizar tareas que, por espíritu conservador, se siguen realizando. Este es el caso típico de informes que se siguen realizando aunque los “clientes” de dichos informes consiguen la información a través de los sistemas informáticos. Piense en materiales o documentos que Usted conserva en su puesto de trabajo. ¿Cuántas veces los utiliza al día? ¿o al mes o al año?
7.4.2 Aproximar tareas relacionadas y físicamente separadas
También es posible que al representar el proceso mediante su layout hayamos podido comprobar cómo algunas tareas sucesivas se realizan en lugares diferentes, exigiendo tiempo y recursos para transportar los elementos del proceso, sean materiales, documentos, etc. La especialización, tanto de las instalaciones como de las funciones organizativas hace que determinadas máquinas, equipos o personas, se agrupen en espacios físicos diferenciados, todo ello con el fin de optimizar el funcionamiento local (máquina o persona), sin tener en cuenta la globalidad del proceso. Así es fácil encontrar que todo el personal de recursos humanos está ubicado en una planta, todas las fotocopiadoras están en la zona de reprografía o todos los hornos están en la zona caliente de la nave. Al enfocar el estudio del proceso de forma global se ponen de relieve estos movimientos que se pueden evitar cambiando la ubicación de las instalaciones o de las personas, de forma que los recursos se acomoden al proceso, no el proceso a los recursos.
7.4.3 Agrupar tareas repartidas
De forma similar a la anterior, con independencia de la separación de espacios físicos, también es habitual que la especialización organizativa o funcional haya originado que las tareas del proceso estén fragmentadas entre diferentes departamentos o especialidades, aspecto que habremos podido comprobar en el diagrama de flujo funcional. En los distintos sectores de actividad se producen situaciones típicas de este tipo de especialización de tareas, así un soldador solamente suelda, o un vendedor solamente vende. A veces la especialización es necesaria pero no siempre está justificada, especialmente en sectores de servicios donde la presencia del cliente en las instalaciones debiera favorecer posiciones más polivalentes.
7.4.4 Equilibrar actividades
También es posible que al medir las actividades del proceso hayamos comprobado que algunas actividades tienen tiempos unitarios diferentes, por tanto, no van al mismo ritmo, lo que origina grandes tamaños de lote o esperas por las tareas lentas. Una alternativa de mejora en estos casos consiste en combinar varias tareas “cortas,” en la medida que estén físicamente próximas (no requieren transportes) y sean interdependientes. De esa forma se puede llegar a una “multitarea” cuyo tiempo unitario sea próximo al ritmo general del proceso. Otra posibilidad es compartir tareas “largas” entre varios recursos, en la medida que al hacerlo se pueda reducir el tiempo unitario y aproximarlo al ritmo del proceso. La flexibilidad y la polivalencia de los recursos e instalaciones son clave para conseguir este tipo de mejoras en cualquier tipo de empresa, sea de producción o de servicios.
7.5 Estandarizar las actividades
Otro grupo de causas de variación o de defectos suele estar asociado a la falta de estandarización de las tareas. Cada persona realiza las actividades de la mejora forma que cree, pero de forma diferente entre unas personas y otras, lo que origina diferentes resultados del proceso. Las soluciones en estos casos se centran en estandarizar las actividades, creando y formalizando las instrucciones, criterios de actuación, registros, etc., necesarias para asegurar que las diferentes personas o grupos que intervienen en las actividades del proceso tienen una forma de actuar similar.
- Procedimientos o especificaciones de trabajo
- Instrucciones operativas
- Criterios de actuación formalizados
- Registros de actividades
- …
7.6 Pensamiento creativo
Otro tipo de causas que necesitan alternativas de cambio son las que responden a problemas internos de algunas de las tareas, cuya respuesta presenta defectos, fallos, averías, errores, etc., que necesitan una solución práctica. La clave del pensamiento creativo es no permitir que ninguna de las “reglas” que rigen la situación actual (pasos del proceso, normas de actuación, comportamientos, formularios, etc.) obstaculicen al equipo de mejora. El equipo debe cuestionar con decisión cada elemento de la situación actual e intentar descubrir aquellos supuestos o reglas que, si se incumplieran, podrían originar una solución innovadora. Utilizar preguntas como las indicadas, es una herramienta útil para encontrar soluciones alternativas al “status quo” del proceso, que mejorarán su resultado, evitando defectos o reduciendo desperdicios.
- Quién realiza el trabajo – ¿puede realizarlo alguien más?
- Dónde se realiza el trabajo - ¿se puede hacer en otro sitio?
- Cuándo se realiza el trabajo - ¿se puede cambiar la secuencia de tiempos?
- Qué recursos requiere el trabajo - ¿en qué otros sitios se pueden encontrar los recursos? ¿Qué más se puede utilizar?
- En qué condiciones se realiza el trabajo - ¿se pueden cambiar?
- Cómo se controla el trabajo - ¿cuál es el valor añadido?
- Qué necesita en realidad el cliente -¿cómo está el cliente utilizando el producto o servicio?
7.7 Benchmarking
Otra alternativa para identificar posibles soluciones prácticas a problemas concretos se basa en la comparación. A veces dentro de la propia organización y otras veces fuera de la misma, existen unidades que realizan procesos similares al que se pretende mejorar, con resultados adecuados. Algunas empresas excelentes publican sus “formas de hacer las cosas” en revistas especializadas, otras las divulgan en foros de excelencia, etc., que son otra fuente de información a tener en cuenta. Cada vez con mayor frecuencia las empresas aprenden unas de las otras utilizando el Benchmarking como herramienta estructurada para compartir prácticas y resultados. En lo relativo a la mejora, teniendo en cuenta que conocemos el proceso a mejorar y su problemática, la técnica de Benchmarking se estructura en tres pasos:
- Identificar el “benchmark” es decir, la empresa u organización que gestiona eficaz y eficientemente el proceso equivalente.
- Analizar cómo gestiona dicha organización el proceso, qué flujo, qué actividades, qué recursos, etc., e identificar las prácticas oportunas para nuestro proceso.
- Adaptar e integrar dichas prácticas a nuestro proceso, e incluso, mejorarlas.
7.8 Work-Out
La técnica de Work-out es una forma estructurada de plantear una reunión de trabajo en la que se buscan soluciones de mejora de un proceso preguntando a las personas que lo conocen más y mejor. La cuestión es tomar decisiones rápidas y consensuadas. Los pasos a considerar en una sesión work-out son:
- definir los objetivos de la reunión
- recopilar las preguntas adecuadas
- identificar y convocar a las personas que participarán en la reunión
- realizar la reunión
- recopilar y evaluar las soluciones de mejora surgidas en la reunión
- comunicar las conclusiones de la reunión y las acciones de mejora que se van a aplicar.
Como herramienta en esta fase de mejora de un proyecto, el workout es una herramienta sencilla pero eficaz. Se trata de organizar una reunión, planteada sobre un aspecto concreto para mejorar el proceso (actuar sobre las causas) y con una preparación previa mediante la cual, a partir de las conclusiones obtenidas en las fases de Medir y Analizar, se plantean preguntas sobre cómo solucionar el aspecto de mejora seleccionado. Los participantes son las personas que intervienen en el proceso, bien sea como agentes o implicados o como partes interesadas y la sesión, de unas 2 a 4 horas de duración, consiste en una tormenta de ideas estructurada para dar respuestas a las preguntas. Para mejorar el resultado de la reunión, las preguntas se pueden enviar con antelación suficiente a los participantes para que preparen sus respuestas. La sesión estará moderada por el Champion o el Black Belt y, tras ella, es conveniente comunicar los resultados a los participantes, con objeto, por una parte, de reconocer su participación y, por otra, de hacerles saber las conclusiones a las que se ha llegado y las acciones de mejora que se van a probar o implantar.
7.9 Técnica de evaluación de riesgos
La evaluación del riesgo de una solución se realiza bajo el punto de vista de las partes afectadas por el proceso:
- Los clientes, para analizar si la solución que se plantea puede tener algún efecto negativo en el cliente.
- Los asociados que participan en el proceso, para comprobar que la solución será aceptada y no afectará al entorno de trabajo.
- Las partes interesadas, para asegurar que la solución se integra en los “sistemas” de la organización y no va a suponer un impacto importante para los objetivos generales.
- Adicionalmente es preciso analizar si la solución puede afectar a aspectos relacionados con el cumplimiento de normas, regulaciones, etc., que estén vinculadas al proceso.
Los riesgos se evalúan bajo dos aspectos:
- se trata de analizar la “calidad” de la solución, en el sentido de si no va a implicar elementos no previstos que pongan en peligro su aplicación y,
- se tratan de evaluar las posibles resistencias a su aplicación.
En la Tabla 7.1 se presentan posibles preguntas clave a cuestionar a clientes, asociados, dirección y relativos al cumplimiento de nuevas medidas propuestas.
Calidad técnica | Aceptación/Resistencia | |
---|---|---|
CLIENTES | ¿Nos arriesgamos a exponer a los clientes a defectos potenciales? | ¿Aceptarán los clientes el cambio? |
ASOCIADOS | ¿Afectará el nuevo proceso a la seguridad de los asociados? | ¿Aceptarán los asociados el cambio? |
DIRECCIÓN | ¿Afectará el nuevo proceso negativamente a los objetivos del negocio como son los costes o el calendario? | ¿Han aceptado el cambio los principales interesados del negocio? |
CUMPLIMIENTO | ¿Existe algún problema de cumplimiento? | ¿Aceptarán y seguirán las personas los nuevos procedimientos? |
7.10 AMFE
El Análisis de Modo de Fallo y Efecto, en su aplicación a la mejora de los procesos, es un método sistemático para identificar las causas de los posibles fallos en el funcionamiento del proceso y para evaluar el riesgo para su resultado (salida).
En los proyectos de mejora Seis Sigma se suele utilizar el AMFE para evaluar las posibles alternativas de mejora cuyas causas están asociadas a fallos en alguna de las etapas de desarrollo del proceso y, en su caso, seleccionar las mejoras que contribuyan a reducir, en mayor medida, el riesgo del proceso. También se puede utilizar como herramienta de apoyo para la identificación y selección de las causas de fallo, si bien la metodología Seis Sigma incluye ya otras herramientas para la selección y comprobación de causas de variabilidad o de fallos.
Como características básicas de este análisis, el AMFE fue desarrollado en los años 60 por la industria aeroespacial, bajo el programa Apolo; es objeto de la norma MIL-STD-1629 (1974) de la Marina de los EEUU. Fue incorporado a principios de los 70 por la industria de automoción y aplicado al análisis de fiabilidad, y está estandarizado actualmente en las normas SAE J-1739 y en la Guía QS-9000 para diseño y mejora de productos y procesos.
A partir de la PLANTILLA AMFE, podemos comentar cada uno de sus elementos.
El primer paso en este análisis es el de identificar los distintos modos de fallo potenciales involucrados, entendiendo por Modo de Fallo cada una de las maneras en que un paso del proceso puede fallar, o cada una de las posibles deficiencias o defectos de su salida (intermedia). A continuación se identifican las causas probables y los efectos sobre el resultado del proceso, de cada modo de fallo.
Una vez identificados estos elementos, el análisis requiere cuantificar, para cada modo de fallo los siguientes factores, ilustrados en la Figura 7.1:
- la frecuencia con que ocurre o se presenta la causa del fallo (variable OCURRENCIA=OCU)
- la severidad o gravedad de las consecuencias (efectos) del fallo (variable SEVERIDAD=SEV)
- la capacidad de detección (variable DETECCIÓN=DET), esto es, la posibilidad que los mecanismos de control del proceso actual sean capaces de detectar el fallo antes de que tenga consecuencias para el cliente.
La combinación de los tres impactos, OCU, SEV y DET, permite obtener un número llamado prioridad de riesgo, NPR. Las causas que suponen mayor prioridad de riesgo deben ser consideradas para definir acciones que contribuyan a reducir la posibilidad del fallo.
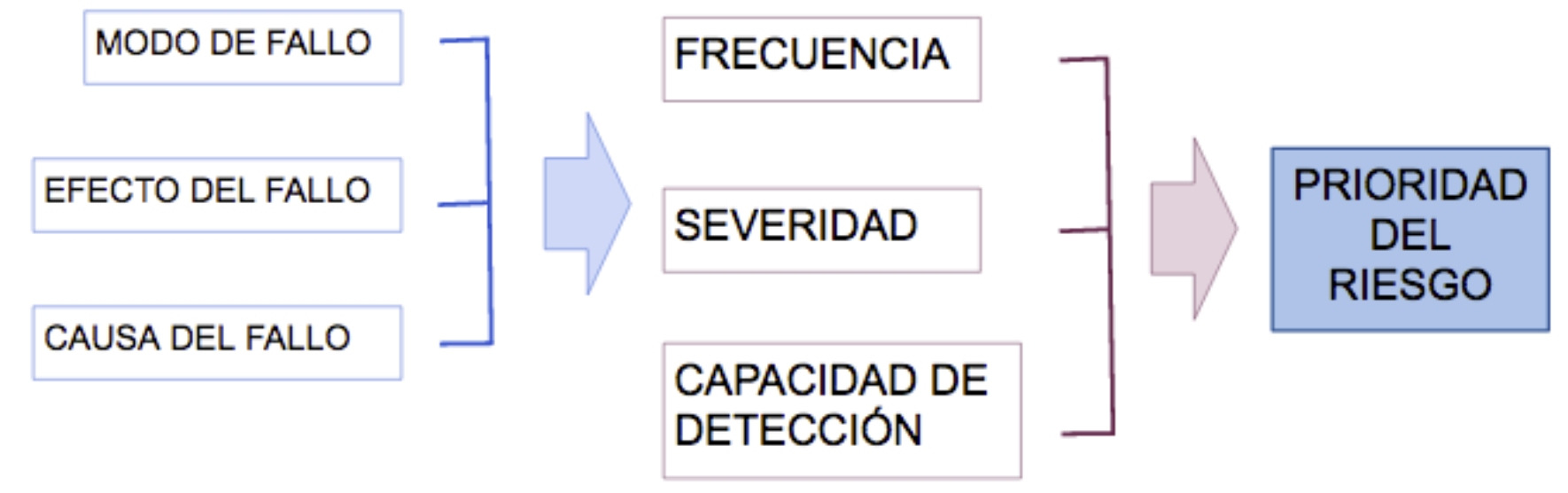
Figura 7.1: Esquema de la dinámica AMFE
La mecánica del AMFE es sencilla, pero requiere un conocimiento importante del proceso, por eso proponemos utilizarla en esta fase, después de la medición y análisis, cuando el grado de conocimiento del proceso es máximo.
Un análisis AMFE se resuelve a modo de tabla con las siguiente columnas en las que cumplimentar información:
- PASO O ETAPA DEL PROCESO. Relación de los pasos o etapas del proceso que pueden originar el fallo (mapa).
- MODO DE FALLO POTENCIAL. Lista de los posibles modos en que el paso del proceso puede fallar. Su funcionamiento no satisfará los requisitos del proceso.
- EFECTO DEL FALLO POTENCIAL. Efecto de cada posible fallo en el cliente o en el resultado final del proceso (cada Y).
- SEV (Severidad). Valor de la gravedad del efecto en el cliente o producto.
- CAUSAS POTENCIALES. Identificación de cada una de las causas potenciales de cada modo de fallo. Cada causa se asocia a un input o variable de funcionamiento del proceso
- OCU (Ocurrencia). Expresada en términos de probabilidad de que se produzca la causa.
- CONTROLES ACTUALES DEL PROCESO. Relación de los controles actuales que actualmente se emplean para prevenir la causa o detectarla cuando se presenta.
- DET (Detección). Valor de la eficacia del control para detectar la causa.
- Número Prioritario de Riesgo, NPR, calculado como \(NPR= SEV \times OCU \times DET\).
Como norma de actuación estandarizada, podemos seguir los siguientes pasos para realizar el análisis de modo de fallo y efecto:
En primer lugar relacionaremos aquellos pasos del proceso en los que se originan los fallos que afectan a nuestra \(Y\) o \(Y\)’s y que ya hemos comprobado.
El segundo paso consiste en identificar la forma en que dicho paso puede fallar, sea incumpliendo requisitos, adoptando valores diferentes de los establecidos, etc.
El tercer punto es evaluar las consecuencias del fallo en el resultado final o \(Y\) del proceso, asignando un valor a la gravedad o severidad del efecto, SEV. En la Tabla 7.2 se proporciona un ejemplo de posible valoración del índice de severidad para un fallo plausible.
Efecto | Severidad o gravedad del efecto | SEV |
---|---|---|
Muy importante | El fallo puede suponer un peligro para la seguridad o una no-conformidad respecto a requisitos legales. Afecta a todo el resultado del proceso. | 9-10 |
Importante | El fallo supondrá alto grado de insatisfacción del cliente. Puede afectar al resto del proceso. Origina reclamación del cliente. | 7-8 |
Moderado | El fallo provoca cierta insatisfacción en el cliente, pudiendo originar una reclamación. Es necesario modificar “algo” para ajustarlo. | 4-6 |
Débil | El fallo incomoda al cliente, pero sin llegar a originar una reclamación. No será necesario modificar el resultado para ajustarlo. | 2-3 |
Menor | El fallo pasará desapercibido para el cliente, no afectando al resultado del proceso | 1 |
- El quinto paso consiste en indicar la causa (o causas) que pueden producir el fallo, a partir de las conclusiones obtenidas en la fase de analizar (causas probables). Una vez seleccionada la causa (o causas) se le asigna a cada una un valor OCU, relacionado con la probabilidad de que se produzca. Esta probabilidad puede estar basada en los datos que hemos manejado en la fase de análisis o en la experiencia sobre el funcionamiento “histórico” del proceso, sea a partir de los datos disponibles o a través de la “apreciación cualificada” de los miembros del equipo, que conocen suficientemente el proceso. En la Tabla 7.3 se proporciona un ejemplo de posible valoración del índice de ocurrencia para cierto evento que produce fallos.
Probabilidad | Descripción | OCU |
---|---|---|
Muy elevada | El fallo (por esta causa) es casi inevitable. El proceso tiene establecidas tareas suplementarias para corregir o compensar el fallo. | 9-10 |
Elevada | El fallo (por esta causa) se produce regularmente. El proceso tiene previstas las tareas suplementarias que se han de realizar para corregirlo. | 7-8 |
Moderada | El fallo (por esta causa) se produce ocasionalmente. No hay tareas suplementarias específicamente previstas. | 4-6 |
Débil | El fallo (por esta causa) se produce de manera aislada, poco significativa. | 2-3 |
Despreciable | El fallo (por esta causa) es improbable. No hay experiencia para decir que se produce. | 1 |
- Luego se evaluarán los controles o mecanismos que tiene actualmente establecidos el proceso y que permitan detectar que se va a producir el fallo o, en el peor de los casos, que se ha producido. A continuación se valora la eficacia DET de este control para detectar la causa y evitar/reducir los defectos. Cuanto antes permitan detectarla, más eficaces serán los controles, hecho que vendrá relacionado con valores bajos en el índice DET. En la Tabla 7.4 se proporciona un ejemplo de posible valoración del índice de detección para detectar fallos con cierta medida de control.
Detección | Descripción | DET |
---|---|---|
Imposible | Los controles actuales no permiten detectar la existencia del fallo. El fallo originará, inevitablemente, las consecuencias. | 10 |
Incierta | Los controles actuales apenas permiten detectar la existencia del fallo. El cliente percibirá seguramente las consecuencias. | 9-8 |
Moderada | Los controles actuales son capaces de detectar el fallo a proceso completado, pero antes de que las consecuencias afecten al cliente. | 7-5 |
Elevada | Los controles actuales son capaces de detecetar el fallo antes de que el proceso haya terminado. Se pueden evitar las consecuencias. | 4-3 |
Muy elevada | Los controles actuales detectarán con seguridad el fallo antes de que el proceso haya terminado. No se producirán las consecuencias. | 2-1 |
- Finalmente, la combinación de los tres impactos, multiplicando los valores asignados en cada uno, permite obtener un número llamado prioridad de riesgo (NPR en la tabla AMFE); valores altos implicarán mayor riesgo. La causas que aportan mayor prioridad de riesgo deben ser consideradas para definir acciones que contribuyan a reducir la posibilidad del fallo.
Las escalas de valoración de Severidad, Ocurrencia y Capacidad de Detección habrán de establecerse previamente. Estas escalas serán específicas para los fallos de productos o procesos en cada proyecto de mejora.
En la Figura 7.2 se ilustra un análisis AMFE para un proceso de fabricación de pan.
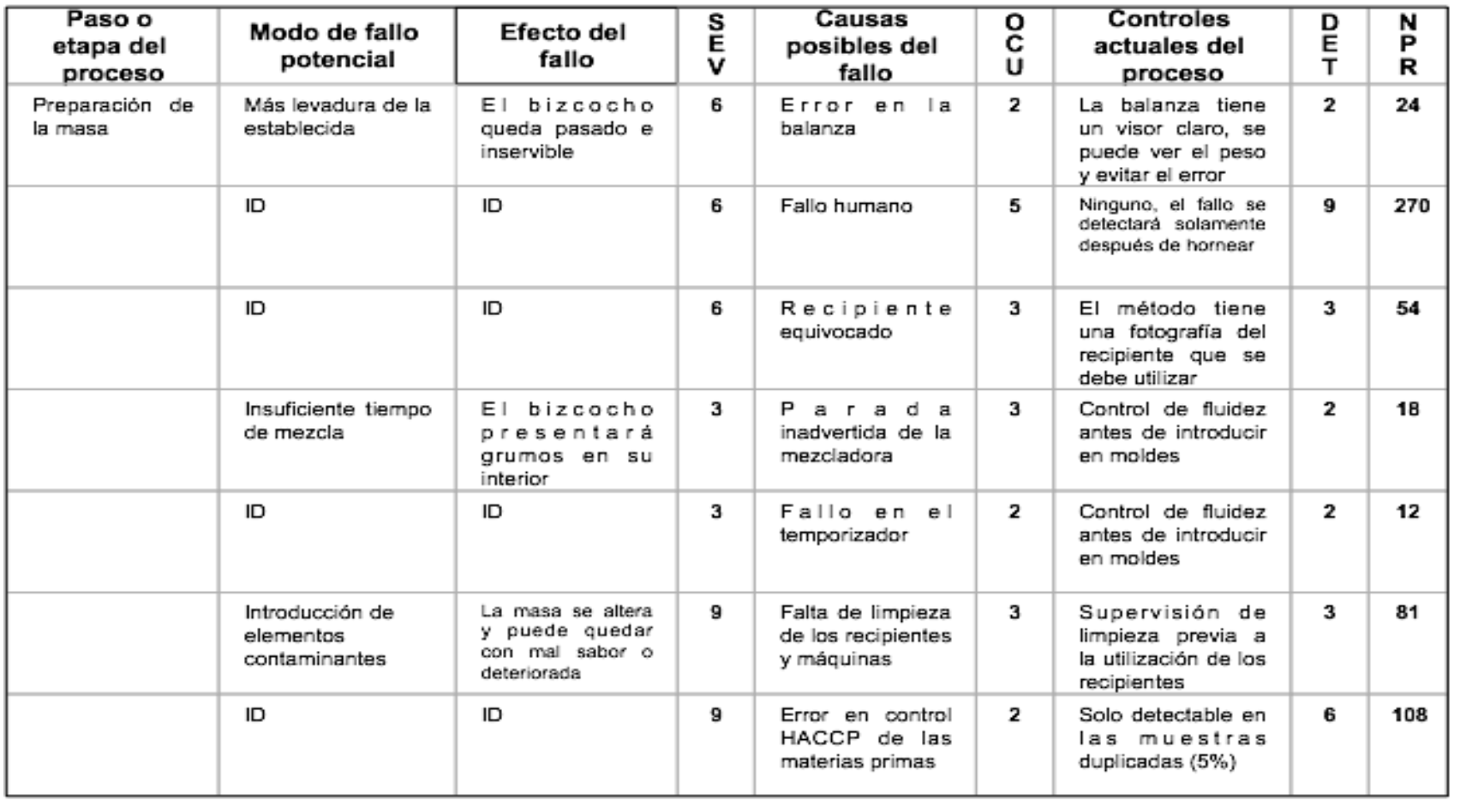
Figura 7.2: Análisis AMFE en un proceso de fabricación de pan. Primera etapa: preparación de la masa.
Para completar el AMFE, y ante una alternativa de mejora propuesta, actualizaremos la información añadiendo el análisis AMFE sobre la nueva propuesta, para verificar que efectivamente reduce el NPR, o decidir entre alternativas si son varias las alternativas de mejora propuestas:
- SOLUCIÓN O ACCIÓN DE MEJORA RECOMENDADA, así como su responsable y una planificación para comenzar a implantarla.
- SEV-OCU-DET actualizado. Nuevos valores de la severidad, de la ocurrencia y de la detección, previstos tras la implementación de dicha acción de mejora/solución.
- NPR actualizado. Nuevo valor del riesgo tras la solución.
Una vez indicada la solución o soluciones que se han identificado antes, teniendo en cuenta el tipo de fallo y la causa o causas que lo producen, es preciso tener en cuenta que dichas soluciones pueden contribuir a:
- Reducir la severidad en el efecto del fallo, evitando o reduciendo la cantidad de “defectos” que se producen o mitigando sus consecuencias.
- Reducir la ocurrencia del fallo o de la aparición de las causas que lo originan
- Aumentar la eficacia de los métodos de control para que se pueda detectar el fallo lo antes posible.
- En cualquier caso, será necesario asignar nuevos valores a cada uno de los factores y calcular el nuevo número de prioridad de riesgo.
- La “cantidad” de reducción de riesgo puede ser un factor a tener en cuenta a la hora de seleccionar soluciones, entre varias alternativas.
7.11 Pruebas piloto
Las pruebas piloto son pruebas de una solución, a pequeña escala, para conocer mejor sus efectos y descubrir cómo hacer más efectiva su aplicación a gran escala. El proceso real es el mejor modelo para sí mismo. Si se es práctico, los experimentos se deben realizar sobre el proceso real.
En las pruebas piloto básicamente tenemos dos opciones:
Probar elementos aislados de la solución (en diferentes secciones de la empresa). Como por ejemplo, una aplicación en una empresa de un nuevo sistema de comunicación entre empleados; se prueba en varios departamentos para evaluar su funcionamiento y reajustar fallos.
Probar soluciones completas. Por ejemplo, se ha desarrollado un nuevo flujo de proceso para las llamadas recibidas en una centralita; para medir el efecto total de la solución, se necesitará evaluar todo el sistema.
7.12 Simulación
La simulación consiste en desarrollar un modelo matemático que describa las relaciones y las interacciones entre las variables de entrada, funcionamiento y salida del proceso. (Y’s y X’s). La utilización del modelo permite crear una historia artificial del funcionamiento del proceso y, sobre todo, evaluar el resultado del proceso al modificar las condiciones de entrada o las variables de funcionamiento, es decir, predecir el comportamiento del proceso en diferentes condiciones. Uno de los modelos que se utilizan para la simulación se basa en los diagramas de flujo y relaciones entre las tareas. En el mercado existen paquetes ya configurados que permiten realizar simulaciones en diferentes condiciones de las variables del proceso.
7.13 Ventana esfuerzo-beneficio
Finalmente, si se ha llegado a este punto con varias posibles alternativas de solución, todas ellas viables, el último paso será seleccionar la o las que parecen mejores teniendo en cuenta el beneficio que producirán y el esfuerzo o coste que puede suponer su implantación. Para ello proponemos un análisis de ventana simple, como el representado en la Figura 7.3.
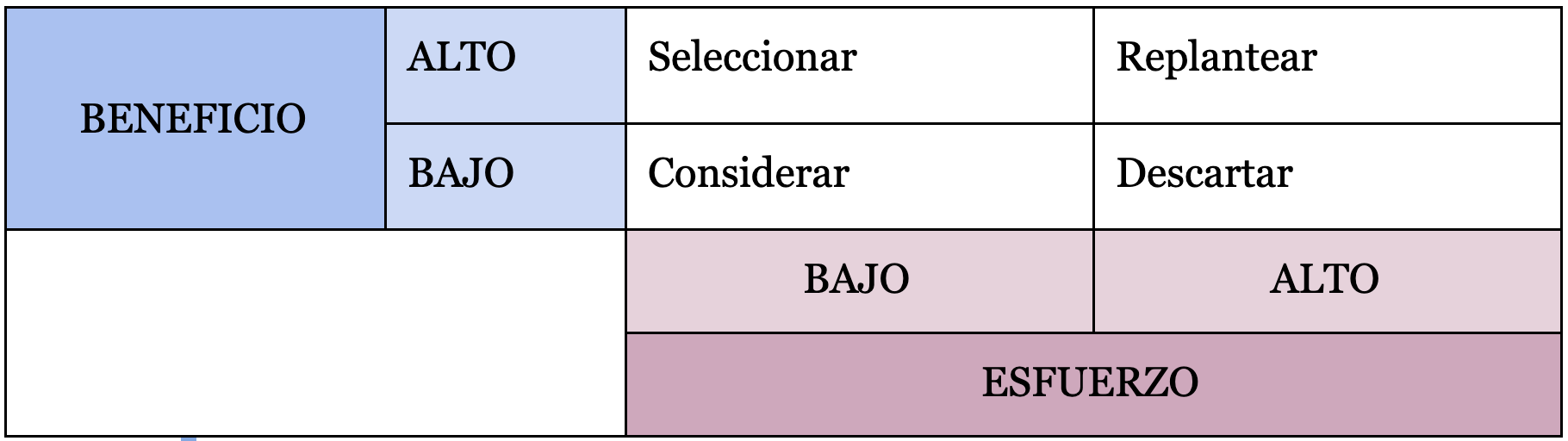
Figura 7.3: Tabla esfuerzo-beneficio. Evaluación de diversas soluciones de mejora.
Las conclusiones serán las que se derivan en función de las especificadas en las celdas en que se encuadre la clasificación lograda en base al esfuerzo (bajo/alto) y el beneficio esperado (bajo/alto).
7.14 Técnica 5S
El nombre de 5S viene de las 5 técnicas implicadas que, en japonés, comienzan con la letra “S.” Como tantos otros enfoques o métodos de gestión que provienen de Japón, se trata simplemente de “sentido común,” pero puesto en orden y con disciplina. Este sentido suele ser, muchas veces, “poco común” en las organización y en el trabajo.
- Suprimir (Seiri) lo no necesario. Clasificar las cosas conforme a su necesidad y quedarnos con las necesarias siempre o frecuentemente.
- Ordenar (Seiton) lo necesario Para evitar errores, fallos o retrasos al realizar las tareas. Sistematizar la colocación de objetos y señalizar.
- Limpiar (Seiso) Establecer rutinas de limpieza/revisión para contribuir al orden y descubrir desajustes, faltas o roturas que pueden originar defectos.
- Estandarizar (Seiketsu) la aplicación sistemática y rutinaria de las técnicas anteriores.
- Mantener (Shitsuke) y supervisar diariamente para asegurar que los estándares se están aplicando según lo previsto.
7.14.1 Suprimir
La primera técnica es suprimir todo aquello que no es necesario para el desarrollo de la tarea o proceso. Las personas tenemos la tendencia a conservar cualquier cosa “por si acaso” tiene utilidad en algún momento. Esta tendencia suele acentuarse cuando se trata de documentos, originando voluminosos archivos (informáticos o físicos), puestos de trabajo abarrotados con montañas de papeles o carpetas, la mayor parte de los cuales no se utiliza, pero que dificultan la búsqueda del elemento que es necesario. Utilizar instrucciones obsoletas (que se conservan) cometiendo errores, consumir tiempo en localizar el aparato, herramienta o documento necesarios entre la maraña de cosas disponibles, confundir un dato “parecido” al necesario localizado entre los que tenemos a mano, etc., son algunas de las causas que pueden introducir “ruido” en el funcionamiento del proceso, alargando las tareas, produciendo desperdicios o causando variación y defectos. La técnica nos propone utilizar el sentido común para clasificar las cosas de acuerdo con el grado previsible de su necesidad. Las cosas que son necesarias siempre o frecuentemente son las que hemos de conservar “a mano,” mientras que las que se utilizan ocasionalmente deben conservarse, pero sin que ello suponga una incomodidad o interferencia para el trabajo. Para eso están los archivos o armarios. Las cosas que, previsiblemente, no se van a utilizar nunca es mejor desecharlas y, en todo caso, ubicarlas en un espacio (almacén o archivo) centralizado, para conservarlas si fuera necesario para otras actividades.
7.14.2 Ordenar
La segunda técnica, una vez que hemos eliminado las cosas no necesarias, es ordenar las cosas necesarias. El desorden es, frecuentemente, una causa de los errores, fallos o retrasos que se producen al realizar las tareas. Dicho desorden se refiere no solo a los elementos físicos (herramientas, materiales, documentos, etc.) necesarios, sino también a los registros informáticos. ¡Cuántas veces somos incapaces de encontrar un archivo que tenemos la seguridad de haber grabado! Definir un método para conservar las cosas en lugares donde sea fácil encontrarlas y ser sistemático a la hora de conservar las cosas. Señalizar los espacios donde se conservan las cosas de modo que sea obvio o fácil identificarlas. En definitiva, ordenar el puesto de trabajo, facilitará realizar las tareas, evitando movimientos no necesarios y reduciendo el tiempo necesario para encontrar las cosas.
7.14.3 Limpiar
La tercera técnica, limpiar regularmente el entorno de trabajo, es más propia de los procesos de manufactura, aunque también podemos observar “puestos” de trabajo mejorables en la prestación de servicios. La limpieza, además de contribuir al orden, permite descubrir posibles elementos que, de mantenerse, pueden originar problemas en el proceso. En los procesos en los que se utilizan máquinas o equipos, una limpieza regular de los mismos, permite observar desajustes, faltas o roturas que, después, originarán defectos en el proceso.
7.14.4 Estandarizar
Una vez aplicadas, por primera vez, las tres técnicas anteriores, se trata de estandarizar su aplicación rutinaria y sistemática, es decir, de establecer pautas para realizar, de forma estandarizada, una revisión regular del entorno de trabajo, de las cosas que conservamos, del orden en el que están conservadas y de su limpieza.
7.14.5 Mantener
La última técnica, mantener, se refiere a la supervisión necesaria para asegurar que los estándares anteriores se están aplicando de la manera prevista. En muchas organizaciones, los programas de auditoria, incluyen la revisión de los puestos de trabajo, concediendo la importancia necesaria al orden y limpieza e, incluso, establecen valores numéricos al resultado de la revisión, valores con los que se fijan objetivos y se conceden premios.
7.15 Diseño de experimentos en mejora
El Diseño de experimentos se puede utilizar para planificar experimentos con los que derivar conclusiones sobre cómo se comporta el proceso ante cada uno de las posibles condicionantes que le afectan, y poder elegir condiciones óptimas para los resultados. Es útil aquí porque permite dar respuesta a diversos objetivos:
- Tomar una decisión entre varias alternativas.
- Discriminar entre variables relevantes (vitales) e irrelevantes.
- Identificar las condiciones que conducen a un objetivo.
- Maximizar o minimizar una respuesta.
- Reducir varianza.
- Dar robustez a un proceso.
- Optimizar la respuesta desde diferentes perspectivas.
- Predecir la respuesta en función de los condicionantes.
Los pasos a dar en un Diseño de Experimentos son:
- Determinar el objetivo/s
- Seleccionar las variables y factores a probar, y los niveles de cada factor
- Seleccionar un diseño experimental
- Ejecutar el diseño (realizar el experimento) y recopilar los datos
- Analizar e interpretar los resultados
- Chequear que los datos son consistentes con las hipótesis experimentales. Validar el análisis.
- Utilizar y presentar los resultados, trasladando las conclusiones a la práctica
Es preciso resaltar que las conclusiones que derivemos de un diseño de experimentos estarán restringidas al rango de variación de las variables que hayamos controlado, puesto que fuera de este rango no se tiene evidencia alguna del comportamiento del proceso. El análisis de los datos obtenidos de la experimentación con un determinado diseño experimental dependerán de los objetivos con que se ha propuesto este diseño, y así mismo, este estará condicionado a los objetivos.
7.16 Análisis Coste-Beneficio
El análisis coste-beneficio es una de las herramientas más utilizadas en Six Sigma. Es básicamente una herramienta de decisión que nos permite comparar los puntos positivos (que producen beneficios) con los negativos (que producen costes) de una propuesta de mejora. La evaluación de costes y beneficios permite determinar cómo de viable y exitoso (o inviable y fracasado) puede resultar el proyecto de mejora.
Llegado a este punto, ya hemos podido identificar y confirmar las causas de la variabilidad o de los defectos que tratábamos de reducir, e incluso hemos propuesto y testado acciones de mejora a través del diseño de experimentos, que nos han proporcionado cierta información sobre los resultados que podemos esperar.
Es el momento pues, de revisar los objetivos y los aspectos económicos del proyecto, preguntándonos por las siguientes cuestiones, a las que dará respuesta un análisis de coste-beneficio:
- la viabilidad de los objetivos iniciales: ¿podremos alcanzar los objetivos, teniendo en cuenta los resultados de las acciones de mejora que hemos conseguido probar?
- la solución total o parcial del problema: ¿se ha resuelto el problema en su totalidad, o sólo hemos resuelto una parte?
- los beneficios a obtener: ¿cuál es el beneficio neto que se puede esperar del proyecto?
7.16.1 Evaluación de beneficios
Cada organización tiene sus parámetros para evaluar los beneficios de un proyecto de mejora. Aquí vamos a indicar algunos elementos de tipo estándar.
En primer lugar debemos tener en cuenta los beneficios tangibles, es decir, aquellos que va a “tocar” la caja de la empresa. Dichos beneficios pueden venir de:
- Un incremento de los ingresos producido por cualquier aumento de la capacidad de producir o del aumento del precio de venta obtenido como consecuencia del proyecto.
- Una reducción de los costes del proceso, sean fijos o variables, producida por cualquier mejora derivada del proyecto.
- Una mejora del flujo de caja, generalmente producida por mejoras del proceso que “aceleran” la consecución de su resultado y, por tanto, la venta y cobro del producto o servicio o por mejoras que “reducen” los inmovilizados necesarios para el proceso. En todos los casos se trata de un dinero que la empresa va a obtener antes de lo previsto.
Por otro lado, aunque no “toquen” caja, los proyectos pueden tener una serie de beneficios que no debemos olvidar, tales como el aumento de la satisfacción de los clientes, asociados, empleados, etc., que seguramente, a medio o largo plazo van a producir resultados tangibles, pero difíciles de estimar. Se trata de los beneficios intangibles.
También es habitual que un proyecto “libere” parte de algún recurso, sea instalación, máquina o persona que, si puede ser empleado para otras actividades (lo que suele quedar fuera del alcance del proyecto), producirá un aumento de ingresos o disminución de costes, pero al margen del proyecto. En la misma situación quedan los proyectos que reducen algún riesgo (fallo, avería, accidente, etc.) que no está asignado a costes y, por tanto, no se puede evaluar el impacto de dicha reducción.
7.16.2 ¿Cómo se realiza un análisis coste beneficio?
Podemos estipular como principales puntos a trabajar en este análisis los siguientes:
- Concretar el período para el que estimar los beneficios y costes.
- Estimar los beneficios que se esperan obtener: ingresos, gastos, flujo de caja.
- Estimar los costes de implantación: inversiones y costes extra con el proceso mejorado.
- Determinar el beneficio económico neto: beneficios-costes.
- Identificar y ponderar los beneficios intangibles.
Concretar el periodo de estudio Un aspecto a tener en cuenta es el “periodo” en el que considerar los beneficios. ¿Cuánto tiempo se debe contabilizar para estimar el beneficio? No hay respuestas fijas. En general si la mejora no requiere inversiones se suele considerar un año completo y si requiere inversiones, se contabiliza por el período de amortización de la inversión. Estimar beneficios En primer lugar debemos estimar los beneficios tangibles esperados, tal como hemos indicado antes, sean incrementos de ingresos, reducción de gastos o mejora del flujo de caja, que deberemos capitalizar de acuerdo con las indicaciones del área económica de la empresa.
Estimar costes de implantación Después será necesario estimar los costes de implantación de las mejoras, tanto las posibles inversiones en equipos, instalaciones, etc., como los costes puntuales que se puedan necesitar para la implantación y los posibles extra costes del proceso mejorado frente a su funcionamiento anterior.
Estimar el beneficio neto La diferencia entre el beneficio que obtendremos con las mejoras y el coste que nos va a implicar su implantación será el beneficio neto del proyecto. Este beneficio, salvo que el área financiera lo estime de otra manera, deberá afectar al presupuesto del ejercicio siguiente, ya sea incrementando ingresos o reduciendo costes de la partida que corresponda.
Identificar beneficios intangibles Finalmente, no olvidemos los beneficios intangibles. Muchas veces el motivo principal para seleccionar un proyecto de mejora no ha sido el resultado económico esperado, aunque se produzca. Son ejemplos de beneficios intangibles la mejora de la satisfacción de los clientes y/o empleados, la liberación de recursos o la reducción de riesgos aun cuando no van vinculados a reducción de costes.
Para la evaluación de la importancia de los beneficios intangibles conviene consultar con el Champion, o solicitar ayuda de área financiera o de la oficina del programa Seis Sigma de la empresa.
En la Figura 7.4 se muestran las relaciones y efectos de los beneficios tangibles e intangibles.
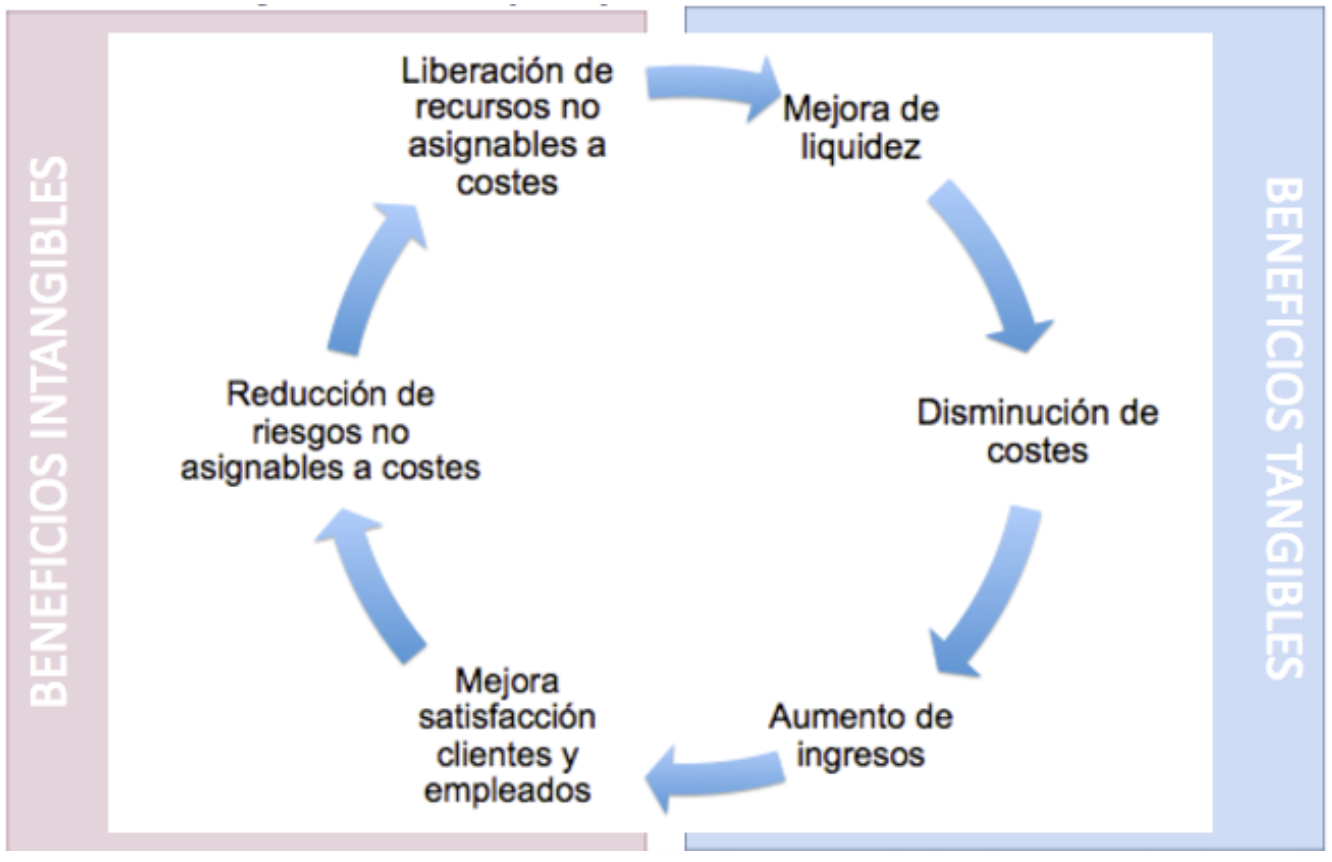
Figura 7.4: Efectos de los beneficios tangibles e intangibles.
7.17 Plan de mejora
Finalmente, para planificar el proyecto cabe realizar las siguientes actividades:
- Resumir las mejoras a plantear, sean alternativas de cambio del proceso o modificación de los factores de funcionamiento del proceso.
- Realizar, en su caso, un estudio coste-beneficio considerando dichas mejoras.
- Plantear al Champion las conclusiones del análisis coste-beneficio, así como a los responsables del proceso.