Capítulo1 Calidad y mejora
1.1 Objetivos de aprendizaje
En este capítulo trabajaremos sobre los siguientes objetivos de aprendizaje:
- Conocer los conceptos básicos relacionados con la calidad y la mejora de procesos y servicios.
- Describir las bases de la metodología Lean.
- Describir las bases de la metodología Seis Sigma.
1.2 Introducción
Antes de desarrollar en detalle la metodología Lean Seis Sigma para la Mejora de Procesos, objeto de este manual, estimamos interesante presentar en este capítulo inicial los conceptos básicos que se refieren a la calidad y la mejora. Introduciremos las metodologías de las que proviene Lean Seis Sigma y complementaremos la información con fuentes externas que pueden ayudar al lector a completar su formación básica sobre la calidad y la mejora.
1.3 Conceptos básicos
Encontramos múltiples definiciones de calidad. Las acepciones que nos proporciona el diccionario de la RAE (n.d.) y que están más relacionadas con el ámbito que nos compete son:
Propiedad o conjunto de propiedades inherentes a algo, que permiten juzgar su valor. Adecuación de un producto o servicio a las características especificadas.
Según la norma ISO9000,
Calidad es el grado en el que un conjunto de características inherentes a un objeto (producto, servicio, proceso, persona, organización, sistema o recurso) que cumple con los requisitos.
En el desarrollo histórico de la calidad -según las premisas en las que la conocemos hoy en día- destacan nombres como Henry Ford a inicios del siglo XX, George Edwards, Walter Shewhart, Armand Feigenbaum, Joseph Juran, Wiliam Deming, Philip Crosby, Kaoru Ishikawa, Koji Kobayashi, y empresas en las que estos personajes desarrollaron sus propuestas como Ford, Western Electric, General Electric, Motorola y Toyota.
En la Sección Enlaces Complementarios se pueden consultar fuentes interesantes sobre Historia de la Calidad.
Un sistema de gestión de la calidad (SGC) integra el conjunto de actividades ordenadas y coordinadas necesarias para evaluar, planificar, ejecutar, controlar y mejorar los elementos de una organización que afectan al desarrollo de una organización.
Las Normas ISO, disponibles en ISO (n.d.), son un ejemplo de sistemas de gestión normalizados, diseñados a través de estándares o requerimientos que han de cumplir las organizaciones para garantizar unos objetivos de calidad concretos en sus procesos, productos o servicios. Actualmente existen más de 19.500 normas ISO desarrolladas en los ámbitos de Calidad, Medio Ambiente, Riesgos y Seguridad, y Responsabilidad Social.
Según ISO 9000 y 9001, en sus Principios para la Gestión de la Calidad (ISO 2015),
Los principios de gestión de la calidad son un conjunto de creencias fundamentales, normas, reglas y valores que se aceptan como ciertas y pueden utilizarse como una base para la gestión de la calidad.
Estos principios los puede utilizar una organización para guiar su proceso de mejora. Los siete principios fundamentales son:
- Foco en el cliente
- Liderazgo
- Compromiso de la gente
- Aproximación al proceso
- Mejora
- Decisiones basadas en evidencias
- Gestión de las relaciones.
Un sistema de mejora es una dinámica implementada en una organización o empresa que consiste en la aplicación de una serie de técnicas cuyo objetivo es la mejora en la empresa, entendiendo como mejora aquello que beneficie el rendimiento de la empresa en alguna de sus formas.
Un sistema de mejora continua busca la eliminación o reducción de las actividades que no aportan valor y que añaden costes a los procesos o servicios de la organización o empresa, y el incremento continuado de la calidad y la productividad, así como de la satisfacción de los usuarios. Se suele relacionar la mejora continua con el método Kaizen.
1.4 Sistema Lean
El sistema de producción Lean, o Lean Manufacturing como también se le conoce, tiene sus orígenes en Toyota, hacia los años 60, en los que la producción eficiente, Just-in-Time, era el único camino para que Japón pudiera competir con la supremacía de Estados Unidos en la producción automovilística. Este sistema de producción es el que ha guiado su integración en los sistemas de mejora continua.
El método Lean para producción y fabricación es una colección de prácticas de negocio, estrategias y métodos que se enfocan en la eliminación de los desperdicios (o desechos) y la mejora continua dentro de la organización. Lean es equivalente a velocidad, y se aplica tanto a procesos de fabricación como a servicios.
La identificación de las actividades con y sin valor añadido, así como de los diversos tipos de desperdicios en un sistema de producción o servicios, son claves para entender el sistema Lean. Veamos en qué consisten estos y qué tipos existen, para exponer a continuación los principios básicos del sistema Lean y la utilidad de las métricas. Acabamos esta sección con una clasificación abreviada de las técnicas y herramientas Lean, que más adelante desarrollaremos de forma particularizada, y con una descripción también breve del sistema de producción pull, que es la base de la aplicación de Lean a la industria y los servicios.
1.4.1 Valor añadido
Considerando la regla de Pareto, que se ha contrastado cierta en multitud de empresas y servicios, el 20% de los recursos/actividades producen el 80% de los desperdicios. Así pues, encontrando y mejorando ese 20% de recursos basura, se conseguirá una reducción importante en los desperdicios y por lo tanto se repercutirá positivamente en los beneficios. En una mejora Lean, se identifican en primer lugar las actividades sin valor añadido para intervenir con prioridad sobre ellas.
El valor añadido de una actividad está vinculado a que el objetivo de esta sea transformar un producto base o materia prima en otro de superior acabado que algún cliente esté dispuesto a comprar. Existen actividades sin valor añadido pero necesarias para el sistema o proceso. Se define “despilfarro” en Lean como todo aquello que no añade valor al producto o que no es absolutamente esencial para fabricarlo.
En el entorno Lean, hoshih (brújula) identifica la eliminación sistemática del desperdicio (todo aquello que resulta improductivo, inútil o no aporta valor sin ser necesario) y se realiza a través de tres pasos:
- Reconocer el desperdicio y el valor añadido en nuestros procesos.
- Actuar para eliminar el desperdicio aplicando la técnica Lean más adecuada.
- Estandarizar el trabajo con mayor carga de valor añadido para, posteriormente volver a iniciar el ciclo de mejora.
1.4.2 Desperdicios
Veamos los tres tipos de desperdicios -a eliminar- que existen en toda organización (proceso o servicio):
Muda representa los restos inútiles, inservibles e inutilizables. El método Lean pretende separar las actividades de valor añadido de las actividades que se reconocen como desperdicios o sin valor añadido.
Mura es el concepto de desperdicio en el sentido de irregularidad. La irregularidad en la carga de trabajo implica innecesarios periodos de baja o estrés de los equipos, sistemas y fuerza de trabajo. La irregularidad redunda en incertidumbre, que da lugar a variación. Además, los intervalos inciertos o irregulares son difíciles de predecir y, en consecuencia, la previsión a futuro resulta complicada. Un alto grado de incertidumbre puede además reducir la capacidad de respuesta, eficacia y eficiencia de la cadena de suministro de una organización.
Muri son los desperdicios creados a consecuencia de una sobrecarga o un fallo en la comprensión de las capacidades. Es un concepto tangible cuando se aplica a la distribución de las instalaciones y los procesos de montaje y manufactura; una carga de trabajo demasiado engorrosa puede provocar fallos o incrementar los ratios de defectos. La sobrecarga en conjunción con las irregularidades puede crear también cuellos de botella costosos en una organización.
Los desperdicios Muda son los más fáciles de categorizar. Casi todas las fuentes físicas de desperdicios dentro de la producción caen en las siguientes fuentes de muda, que pueden resumirse con el acrónimo DOWNTIME, y se muestran explícitas en la Tabla 1.1.
SIGLA | TÉRMINO | SIGNIFICADO |
---|---|---|
D | Defective Production. Producción defectuosa | Los defectos provocan costes tangibles (desperdicios, retrabajo, …) e intangibles (insatisfacción del cliente, pérdida de mercado. |
O | Overprocessing. Sobreprocesado | No hay necesidad de aplicar más procesado a elementos que ya cumplen las especificaciones del cliente. |
W | Waiting. Espera | El tiempo que un componente ha estado esperando en el proceso de fabricación no puede ser facturado al cliente. |
N | Non-Used Employee Talent. Infrautilización del talento | Infrautilizar el talento de los empleados representa costes difíciles de cuantificar, pero a la postre negativos para la organización. La mejora continua alude no sólo a procesos sino también a las personas. |
T | Transportation. Transporte | El transporte que no aporta valor se considera desperdicio. Además, el proceso de mover el producto expone al producto a posibles pérdidas y daños. |
I | Inventory. Inventario | Mantener un inventario disponible ocasiona costes y desperdicio en otras áreas. |
M | Motion. Movimiento | Movimientos innecesarios en el procesado (máquinas, operadores, ..) genera desgastes evitables y reduce eficiencia. |
E | Excessive Production. Producción en exceso | Una producción que supera la demanda puede incrementar defectos y aumentar los costes de almacenaje. |
1.4.3 Principios Lean
Podríamos resumir la filosofía LEAN en estos principios básicos que destaca Sweeney (2017):
1. Visibilidad y eliminación de los desperdicios. Una organización que se compromete con reducir los desperdicios, también se compromete con encontrarlos. Para ello es preciso:
- Visibilizar la organización a todos los niveles para descubrir dónde están los problemas.
- Identificar las fuentes de desperdicios (DOWNTIME).
- Diferenciar entre actividades con valor añadido y actividades sin valor.
2. Estrategia y flexibilidad. Lean tiene que ver con estrategia y planificación en todas las operaciones y niveles en la empresa.
- Implica el compromiso de la dirección y la formación de líderes y equipos multidisciplinares involucrados en la filosofía Lean.
- Con una visión estratégica se definen los objetivos, que conectan y justifican las tareas a emprender.
- La organización está dispuesta y preparada para el cambio (de necesidades, recursos, …).
- La producción está basada en un sistema PULL (se produce a demanda) para evitar la sobreproducción, costes de inventario, almacenaje, …
3. Simplicidad. Las operaciones más simples son más fáciles de implementar, enseñar y monitorear, de modo que los desperdicios y los errores son más fáciles de identificar. En consecuencia:
- Los problemas complejos han de ser descompuestos en otros más pequeños y simples, que tendrán a su vez, soluciones más sencillas.
- Las soluciones más simples son siempre las mejores soluciones.
4. Mejora continua. Lean implica Kaizen, filosofía que supone la creación de una cultura de mejora continua, compendia diversos modos de innovación y gira en torno al concepto de que los cambios frecuentes e incrementales producen resultados estables y duraderos. Un compromiso con la filosofía Kaizen convierte a todos los empleados en motores de innovación que producen resultados a todos los niveles y que en todo momento son receptivos a cambios. Los 10 principios básicos de Kaizen son, según Llamas (2015):
- Abandonar las ideas fijas, rechazar el estado actual de las cosas.
- En lugar de explicar lo que no se puede hacer, reflexionar sobre cómo hacerlo.
- Realizar inmediatamente las buenas propuestas de mejoras.
- No buscar la perfección: basta ganar el 60% desde ahora.
- Corregir un error inmediatamente e in situ.
- Encontrar las ideas nuevas en la dificultad.
- Buscar la causa real, plantearse los 5 porqués y buscar la solución.
- Tener en cuenta las ideas de diez personas en lugar de esperar la idea genial de una sola.
- Probar y después validar.
- La mejora es infinita.
Cuando surgen problemas específicos a resolver y es preciso una “innovación rápida,” se suele utilizar un “kaizen blitz” o “bombardeo kaizen,” que consiste en un evento intensivo para la mejora, en el que se planifican workshops, y se dinamizan entrenamientos y discusiones guiadas sobre el problema a resolver.
La mejora continua no es una actividad puntual, sino el producto de esfuerzos continuados ligados al ciclo PDCA (también conocido como ciclo Deming o ciclo Shewart), siglas que identifican: Plan (marcar objetivos y planear acciones)-Do (ejecutar el plan)-Check (medir las mejoras)-Act (actuar a partir de lo aprendido).
Una actividad Kaizen se secuencia en una serie de pasos sobre los que se opera en conjunción con el método PDCA:
- Estandarizar operaciones y actividades.
- Medir operaciones y actividades para establecer un referente.
- Comparar los referentes para alcanzar los objetivos o requisitos.
- Incrementar la productividad y reducir los desperdicios a través de la innovación.
- Volver a medir para establecer un nuevo referente y verificar un progreso exitoso.
- Reiniciar el ciclo con las operaciones recién estandarizadas.
1.4.4 Métrica Lean
La velocidad en Lean se cuantifica a través de la “eficiencia de ciclo del proceso” (process cycle efficiency), que se define como el cociente entre el “tiempo total de valor añadido” (amount of value-added time), esto es, el trabajo que un cliente reconocería como necesaro para crear el producto o servicio, y el “tiempo total de producción” (total lead time), esto es, el tiempo total que se invierte en la elaboración, desde el principio hasta el final, dado en la Ecuación (1.1).
Eficiencia de ciclo del proceso = Tiempo de valor añadido Tiempo total de producción.
Un proceso Lean tiene un tiempo de valor añadido superior al 25% del tiempo total de producción, esto es, con una eficiencia de ciclo del proceso al menos de 0.25. Cualquier proceso con una eficiencia de ciclo bajo tendrá grandes oportunidades para generar reducción de costes. Incrementar la eficiencia de ciclo de un proceso desde el 5% al 25% supondría una reducción del 20% en los gastos generales (tiempo de producción), que provocarían entonces (por la ley de Pareto) una mejora (reducción de retrasos) del 80%.
La incorporación del sistema de producción Lean reportará diferentes tipos de beneficios vinculados a la reducción de costes:
- disminución de inventarios y reducción de costes de almacenaje, personal y espacios,
- reducción de los tiempos de producción, y en consecuencia de los tiempos de detección de fallos y del retrabajo, así como del tiempo de trabajo de operadores y supervisores,
- reducción de los costes logísticos al evitar acumulaciones de productos y envíos masivos acumulados, así como de los tiempos para vender y conseguir beneficios,
- reducción de los defectos que son distribuidos a clientes y su consecuente disminución, así como el ahorro con las actividades de servicio al cliente.
Existen diversas métricas en Lean que permiten identificar dónde se producen los retrasos o time traps, y qué efecto producen en la producción; al compararlos con la demanda se proponen actuaciones Lean adecuadas que producen reducciones viables con beneficios garantizados. Los sistemas de gestión empresarial del tipo MRP (Material Requierements planning) o ERP (Enterprise resource planning) entre otros, permiten calcular fácilmente estas métricas.
1.4.5 Técnicas Lean
Según Hernández-Matías and Vizán-Idoipe (2013), para tener una visión clara de las técnicas y herramientas Lean, estas se pueden distribuir en tres grupos:
- GRUPO 1: aquellas cuyas características, claridad y posibilidad real de implantación las hacen aplicables a cualquier casuística de empresa/producto/sector.
- Diagnóstico con Mapa de Cadena de Valor (Value Stream Mapping o VSM)
- Las 5S (Seiri, Seiton, Seiso, Seiketsy y Shitsuke)
- SMED (Single Minute Exchange of Dies)
- Estandarización
- TPM (Total Productive Maintenance) o Mantenimiento Productivo Total, y sistemas OEE (Overall Equipment Effectiveness), que relacionan disponibilidad, rendimiento y calidad.
- Control visual.
- GRUPO 2. Aquellas técnicas que, aunque aplicables a cualquier situación, exigen un mayor compromiso y cambio cultural en todas las personas, tanto directivos, mandos intermedios, como operarios:
- Jidoka o autonomización de los defectos.
- Técnicas de calidad: como PDCA (Plan-Do-Check-Act) y TQM (Total Quality Management).
- Sistemas de participación personal (SPP).
- GRUPO 3. Técnicas más específicas y avanzadas, que cambian la forma de planificar, programar y controlar los medios de producción y la cadena logística, asociadas a las técnicas JIT -Just In Time- (Hirano 2002). Exigen de recursos especializados para llevarlos a cabo, como:
- Heijunka (o production leveling) para reducir los desperdicios mura y en consecuencia los muda.
- Kanban, consistente en un sistema de información para la planificación en Lean Manufacturing.
La manera correcta de iniciar una implantación Lean es empezar con un planteamiento modesto basado en pocas técnicas, incluso solo una, partiendo en cualquier caso del compromiso de la empresa de invertir en su personal y promover la cultura de la mejora continua. Cualquier plan de acción debe plantearse a largo plazo, persiguiendo un cambio cultural que pase a formar parte del saber hacer de la empresa.
1.4.6 Producción Pull
La producción Pull es un elemento clave en Lean.
El modelo tradicional de producción, conocido como Push production, está basado en una predicción de la demanda, en base a la cual se proveen las materias primas con las que se alimenta el proceso de producción para obtener los bienes finales, que generalmente siempre se producirán en exceso para ahorrar costes asociados con la economía de escala (esto es, repartir los costes fijos entre más unidades de producción).
En el sistema de producción Pull el foco es el cliente: la producción responde a la demanda del cliente en tiempo real. Esta demanda se utiliza para ajustar el volumen de abastecimiento de materias primas precisas que entran en la cadena de producción. Para que esta producción sea rentable, la producción ha de ser flexible y han de reducirse los costes asociados a los cambios en las líneas/volúmenes de producción. Para reducir el volumen de almacenamiento y garantizar el stock de seguridad, ha de desarrollarse un método de producción e inventario preciso y veloz, conocido como Just-In-Time (JIT), que asegura que la correcta cantidad de bienes llega al lugar correcto en el tiempo correcto.
Cada medida de reducción de los desperdicios y de innovación propuestas con Kaizen, respalda y hace posible la flexibilidad y fortaleza del sistema de producción Pull.
1.5 Mejora Seis Sigma
Six Sigma, en español “Seis Sigma,” o como la reconoceremos en ocasiones a lo largo del libro, 6Sigma, es un sistema de gestión de procesos orientado a la mejora de la calidad, basado en el uso de la Estadística para medir la capacidad, el rendimiento y el funcionamiento de los procesos, y propone unos objetivos concretos de reducción del número de defectos al intervenir en la reducción de la variabilidad de los procesos.
Fue desarrollado por la compañía multinacional de telecomunicaciones Motorola en 1986 y ha evolucionado desde entonces para convertirse en una estrategia de negocio que proporciona importantes beneficios económicos. En 2005, diecinueve años después de adoptar Seis Sigma en su sistema de producción, Motorola declaró haber ahorrado, gracias a este sistema, 17 billones de dólares. En 2011 la International Organization for Standardization (ISO) consolidó Seis Sigma como un proceso de mejora de negocio con la norma ISO 13053:2011.
1.5.1 Principios Seis Sigma
La metodología Seis Sigma podríamos resumirla en 3 principios básicos:
- La calidad de los productos y servicios percibida por los clientes es la clave. La variabilidad produce defectos y los defectos reducen la calidad. Es preciso un esfuerzo continuo en reducir los defectos con fiabilidad, para garantizar cubrir las expectativas de los clientes. Esto se consigue reduciendo la variabilidad.
- Los procesos y servicios tienen características que pueden medirse, analizarse, mejorarse y controlarse. Así pues, la utilización de técnicas estadísticas resulta clave para medir, cuantificar y predecir el funcionamiento de un sistema bajo las condiciones actuales y encontrar las óptimas.
- El objetivo de conseguir mejoras de calidad sostenibles requiere del compromiso de la organización completa, y particularmente del equipo directivo, al que se le pide destinar inversión y recursos humanos que se dediquen a tiempo completo en la mejora.
Es interesante la presentación de Seis Sigma por Editor (2017a), en la que la muestra como un compendio de filosofía, metodología, métrica y conjunto de herramientas.
Para implementar un proyecto de mejora Seis Sigma en una empresa, es imprescindible:
- Focalizar en el cliente, que plantea unos requisitos para comprar el producto. La Voz del Cliente (VOC, voice of the customer) se utiliza para determinar cuáles son los requerimientos específicos y medibles sobre los productos a generar, y decidir cuáles son los más importantes (CTQ, critical to quality).
- Focalizar en los defectos, entendiendo estos como desajustes con los requisitos críticos de los clientes o CTQs.
- La implicación de la dirección de la empresa en el proyecto, integrando a la vez las prioridades estratégicas de la empresa.
- La dedicación de recursos e infraestructuras: habrá de invertirse en la formación de personal de la propia empresa (entre un 1 y un 3%) que pueda dedicarse a jornada completa durante el desarrollo del proyecto, y luego proseguir garantizando el mantenimiento junto al resto de personal vinculado al proyecto bajo diferentes roles. En la Figura 1.1 se ilustran los agentes involucrados en un proceso de mejora Seis Sigma, junto con sus interrelaciones y funciones en dicho proceso.
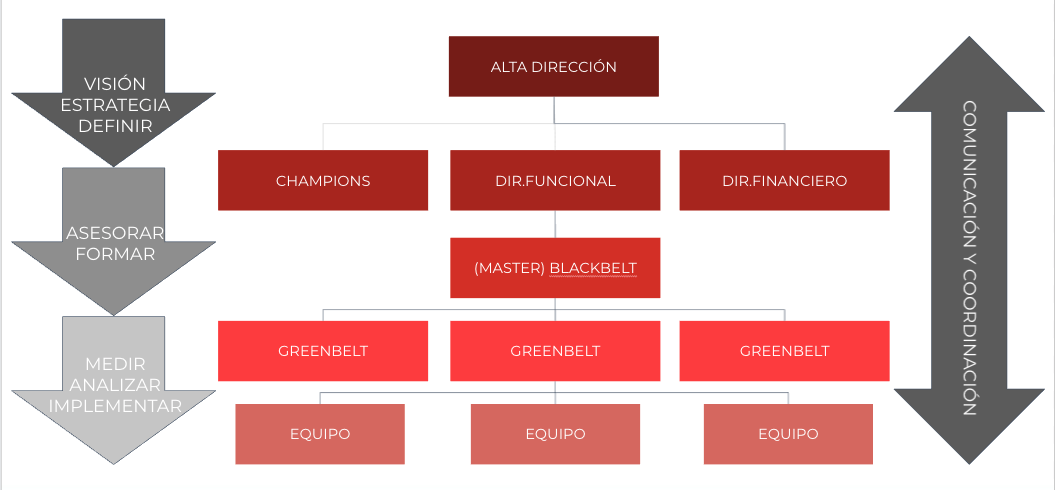
Figura 1.1: Estructura organizativa en un proyecto Seis Sigma.
1.5.2 Defectos y variabilidad
La metodología Seis Sigma está centrada en la reducción de los defectos a través de la reducción de la variabilidad en los procesos o servicios.
En primer lugar, es vital escuchar al cliente (VOC) al respecto de qué tipo de producto y características desea y requiere para convencerse de la calidad del mismo. Estas opiniones se han de plasmar en especificaciones medibles y cuantificables sobre los productos, denominadas requisitos de calidad. Aquellos requisitos que resultan ser los más importantes se denominan requisitos CTQ. Un defecto se define como todo aquello que no cumple con los requisitos CTQ de los clientes. El número de defectos está directamente asociado con la variabilidad de un proceso, de modo que al reducir la variabilidad, se reducen drásticamente los defectos. Es importante entender que los defectos no sólo reducen la calidad percibida, sino que además ocasionan costes por retrabajo, demoras y otras pérdidas asociadas. En la Figura 1.2 se muestra un caso inicial en el que los datos rebasan los límites de especificación (líneas verticales en rojo) dados por los CTQ del cliente y generando por lo tanto defectos; al reducir la varianza, prácticamente todos los resultados plausibles quedan entre los límites de especificación y el número de defectos es prácticamente de cero. Finalmente, al reducir los defectos y controlar la producción bajo los estándares de calidad que satisfacen a los clientes, los beneficios financieros se incrementan considerablemente en la empresa.
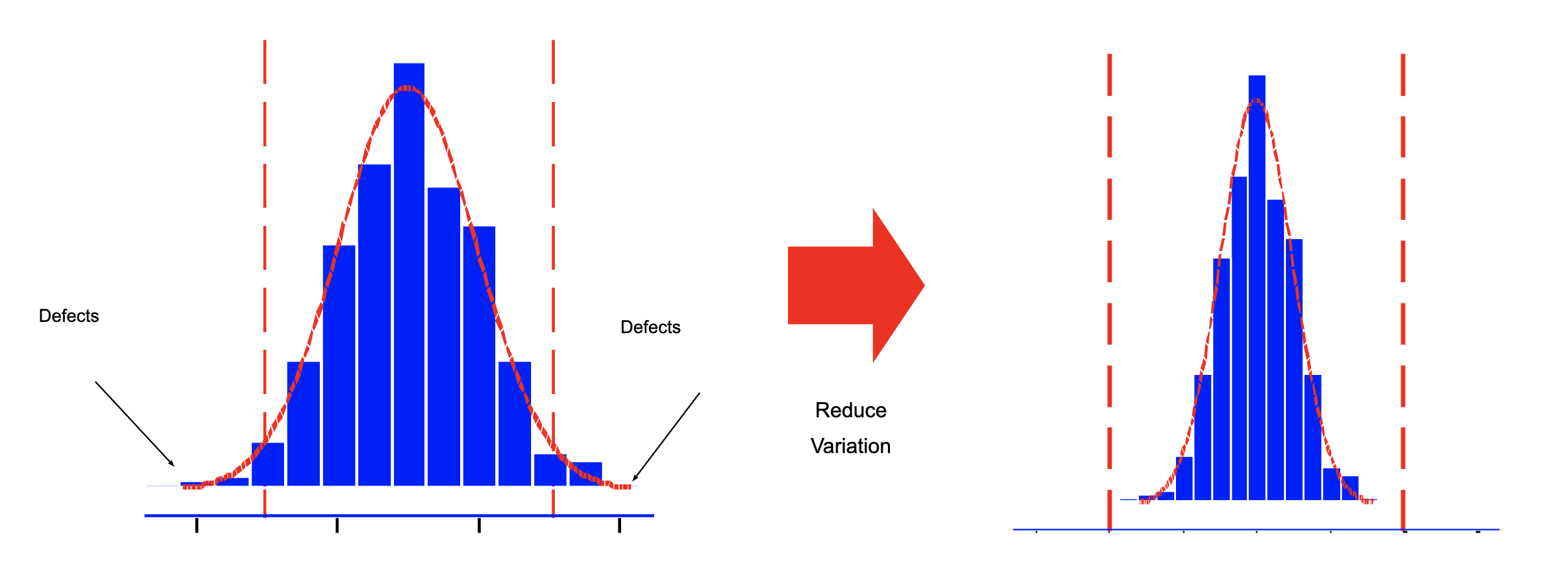
Figura 1.2: Reducción de defectos a través de la reducción de la variabilidad.
1.5.3 Métrica Seis Sigma
Para reducir la variabilidad, es clave identificar las fuentes de variación, aspecto en el que la utilización de datos y técnicas estadísticas es crucial. Para encontrar las condiciones óptimas de funcionamiento de un sistema garantizando los requisitos de calidad, es crucial el diseño de experimentos, otra herramienta estadística que cobra un papel protagonista en un proyecto de mejora Seis Sigma, al ser capaz de generar mejoras inmediatas. Por último, el modo de garantizar la estabilidad en el tiempo de las mejoras es mediante la utilización de técnicas de control estadístico de procesos (CEP en español, y en inglés SPC, Statistical Process Control). Todas estas técnicas estadísticas van acompañadas, en un proyecto Seis Sigma, de protocolos estandarizados de análisis y actuación hacia la mejora que trabajaremos más adelante.
La forma de cuantificar en un proyecto Seis Sigma la proximidad a la excelencia, es a través del nivel sigma. El nivel sigma de un proceso o servicio cuantifica la capacidad del mismo para cumplir con los requisitos CTQ del cliente, y esto se traslada al lenguaje del número de defectos permitidos respecto del volumen de unidades posibles u oportunidades, como el DPMO o Defectos por Millón de Oportunidades (Defects per million of opportunities). El número de incumplimientos con los CTQ que puede tener cada producto/unidad se reconoce como el número de oportunidades. El objetivo en un proyecto Seis Sigma es conseguir un nivel 6σ de defectos, que se corresponde con asegurar un máximo de 3.4 defectos por cada millón de oportunidades, o lo que es lo mismo, un rendimiento (yield) o volumen relativo de buenos resultados, del 99.9997%. Por supuesto, no en todos los procesos/servicios el objetivo ha de ser llegar al nivel 6σ, y podría ser suficiente exigir algún otro nivel de calidad como el 2σ o 3σ, como ocurre habitualmente en la mejora de servicios. En la Tabla 1.2 se muestra, resumida, la relación entre el nivel sigma, los defectos (permitidos) por millón de oportunidades (DPMO) y la probabilidad según una distribución normal de la zona comprendida entre la media y ±i sigmas, siendo i el nivel sigma.
Nivel σ | DPMO | Rendimiento | Dist.Normal |
---|---|---|---|
6 | 3.4 | 99.9997% | 1 |
5 | 233 | 99.977% | 99.9999% |
4 | 6210 | 99.379% | 99.99% |
3 | 66807 | 93.32% | 99.73% |
2 | 308537 | 69.27% | 95.45% |
1 | 690000 | 31% | 68.27% |
1.5.4 Etapas del proyecto
Un proyecto de mejora Seis Sigma sobre un producto o servicio existente, se desarrolla en cinco etapas básicas, denominadas globalmente como DMAIC (Define/Measure/Analyse/Improve/Control):
- DEFINIR (Define), donde se elige y describe qué proceso/s se abordan, cómo se desarrollan en la actualidad, y cuáles serán los objetivos, requisitos, recursos y planificación del proyecto.
- MEDIR (Measure), cuando se recopilan datos para cuantificar la gravedad de las ineficiencias del proceso y su capacidad para conseguir los requisitos marcados.
- ANALIZAR (Analyse). Con los datos se investigan las fuentes de variabilidad o factores críticos para la calidad, cuyo control repercutirá en una reducción de la varianza y en consecuencia del número de defectos.
- MEJORAR (Improve), fase en la que se proponen mejoras concretas en los procedimientos, para cumplir con los requisitos impuestos. En esta fase es importante la aplicación del Diseño de Experimentos para testar soluciones alternativas.
- CONTROLAR (Control), cuando se comprueban las mejoras y se establecen alarmas y protocolos de acción para mantener las mejoras en el tiempo.
En la Figura 1.3 se muestran todas las etapas de un proyecto Seis Sigma, junto con las tareas básicas y objetivos que se desarrollan en cada una de ellas.
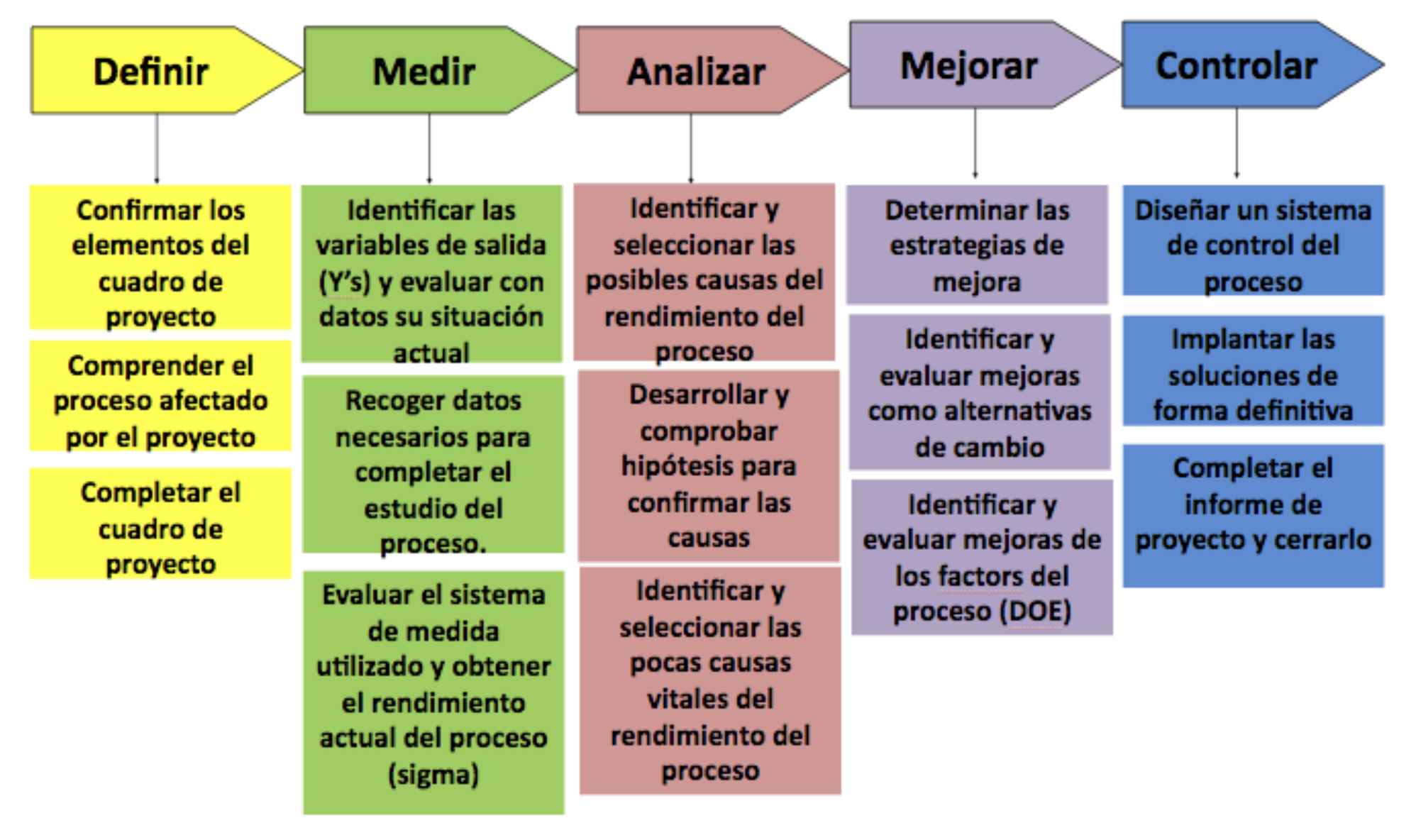
Figura 1.3: Etapas de desarrollo de un proyecto Seis Sigma.
Cuando Seis Sigma se implementa para el desarrollo de un producto o servicio, DMAIC se transforma en DMADV, donde las dos últimas letras aluden a Design (Diseñar, D) y Verify (Verificar, V):
- D (Definir) se define el proyecto.
- M (Medir) se determinan los requisitos y deseos del cliente.
- A (Analizar) se identifican funciones y se generan y seleccionan conceptos.
- D (Diseñar) se desarrolla el diseño, se testan optimizan las componentes y el diseño global.
- V (Verificar) se verifica el funcionamiento del diseño y se implementa.
La tesis de Prieto-Corcoba (2012) aporta mejoras en la metodología DMAIC reforzando la base científica en que se fundamenta Seis Sigma.
1.5.5 Formación Seis Sigma
La formación en Seis Sigma, está completamente estandarizada, sujeta a certificación por organismos y empresas internacionales (basta una rápida búsqueda en Internet), y diferenciada en tres niveles: Yellow, Green y Black Belt, que es el máximo.
Trabajaremos aquí a un nivel “Green Belt.” Las tareas de un Green Belt en el desarrollo de un proyecto Seis Sigma pasan por conocer:
- cómo es un proyecto Seis Sigma y qué beneficios se pueden conseguir aplicándolo
- cómo funciona la metodología de mejora Seis Sigma
- cómo se pueden llevar a cabo con éxito los proyectos Lean Seis Sigma para mejorar los procesos
- cómo utilizar inteligentemente las técnicas y herramientas, tanto las más simples como las estadísticas más sofisticadas
- cómo transferir el proyecto una vez completado.
1.6 Enlaces Complementarios
Se pueden completar conocimientos en las siguientes fuentes:
Rastogi (2018) hace una breve introducción a Lean, Seis Sigma y Lean Seis Sigma, confrontando y complementando intereses.
Hessing (2020) hace un relato histórico sobre los orígenes y generadores de la metodología Seis Sigma.
Ishikawa (1984) es uno de los artículos básicos para la calidad, de manos de un referente como Isikawa.
Juran (1993), considerado uno de los padres y posiblemente el mayor formador en Seis Sigma, escribió un artículo en 1993 para el Washington Post en el que relata los orígenes de la calidad en Japón.
En Network (2011) hacen un recorrido breve de la calidad, destacando figuras claves como fueron Juran y Deming.
En American Society for Quality (n.d.) ofrecen aspectos diversos que definen el Seis Sigma e introducen la metodología Lean Seis Sigma.
Trainer (2013) enfoca el relato de la historia de la calidad hacia la figura de Jack Welch en General Electric.