Capítulo2 Lean Seis Sigma
2.1 Objetivos de aprendizaje
En este capítulo trabajaremos sobre los siguientes objetivos de aprendizaje:
- Describir las bases de la metodología Lean Seis Sigma.
- Recorrer la hoja de ruta en la planificación de un proyecto Lean Seis Sigma.
2.2 Introducción
Presentados en el capítulo anterior los fundamentos de las metodologías Lean y Seis Sigma por separado, profundizamos aquí en la conjunción de las dos, o metodología Lean Seis Sigma. Se da una definición global de la metodología y se introducen los principios, leyes y herramientas básicas que se utiliza en la aplicación de esta metodología para la mejora de los procesos. Se comentan así mismo, diversas consideraciones sobre cómo implementar la mejora, impusarla y acelerarla.
2.3 Qué es Lean Seis Sigma
Una vez expuesto en qué consisten cada una de las visiones Lean y Seis Sigma de forma separada, surge Lean Seis Sigma (en ocasiones la llamaremos Lean6Sigma o L6S) como estrategia óptima, al ser capaz de identificar las mejoras específicas que deben realizarse en una empresa, ordenar su implementación y aplicar las herramientas más eficientes para conseguir los objetivos de mejora con rapidez.
Seis Sigma se fundamenta en la reducción de la variabilidad y de los defectos. Lean se fundamenta en eliminar todos los desperdicios o elementos que son innecesarios en un proceso y que en consecuencia lo ralentizan. Seis Sigma utiliza una buena fundamentación estadística para la medición, análisis y control de la mejoras. Lean integra un buen número de herramientas y técnicas para identificar desechos, implementar con rapidez mejoras con las que reducir tiempos, costes e inventarios, y así aumentar la eficiencia.
Lean Seis Sigma es una metodología que maximiza los beneficios de las empresas al conseguir, al ritmo más rápido, la mejora en la satisfacción de los clientes, costes, calidad, velocidad de los procesos y capital invertido. Es precisa la fusión de Lean y Seis Sigma porque por sí solas no pueden provocar estos objetivos: Lean sola no es útil para medir, analizar y controlar un proceso, y Seis Sigma sola no puede mejorar sustancialmente la velocidad de los procesos o reducir el capital invertido (George 2002).
Es importante tener en cuenta el principio básico de Lean Seis Sigma: las actividades que causan los problemas críticos para la calidad percibida por el cliente y las que provocan los retrasos mayores en cualquier proceso, son aquellas que ofrecen las máximas oportunidades para la mejora en costes, calidad, capital y tiempo de producción.
La clave es resolver en primer lugar los problemas de calidad externa que afectan a los clientes. Los problemas internos de calidad, costes, inventarios y tiempos de producción se manifestarán en los tiempos de retraso que provocan. Calidad y retrasos, si bien no son lo mismo, tienen una estrecha relación, pues el 20% de los desechos provocan el 80% de los retrasos (conocido como el principio de Pareto). Además, una velocidad más rápida en el proceso multiplicará la velocidad a la que las herramientas de calidad reducirán los defectos.
Las preguntas que sólo Lean Seis Sigma puede responder y de ninguna manera Lean o Seis Sigma de modo separado, son:
- ¿En qué pasos del proceso habremos de aplicar primero las herramientas de Lean Seis Sigma?
- ¿En qué orden y hasta qué grado?
- ¿Cómo conseguir más rápidamente las máximas mejoras en costes, calidad y tiempo de producción?
La sinergia de Lean y de Seis Sigma juntas es la que ayuda a las empresas a reducir costes en un 20% y el inventario en un 50% en menos de dos años.
Aartsengel and Kurtoglu (2013) describen una actividad Lean SeisSigma operando a 6 desviaciones estándar alrededor de su valor esperado y que produce resultados efectivos, eficaces y flexibles de la siguiente manera:
“… a business activity operating at a performance permissible limit of variations of 6 standard deviations around its expected central tendency and that is: 1) Effective, producing the desired outcome correctly the first time. 2) Efficient, minimizing the resources used to produce the desired outcome in the shortest time. 3) Flexible or Adaptable, being able to adapt to changing customers and to the circumstances surrounding the business and its market needs.”
La mayor parte del material producido en un proceso de manufactura pasa esperando el 95% de su tiempo previo a la venta: esperando que algún otro proceso le añada valor, como inventario esperando ser vendido,… Al reducir este tiempo de espera en un 80%, los gastos de fabricación y los costes de calidad se pueden reducir en un 20%, adicionales a los beneficios de generar una distribución más rápida y unos inventarios más pequeños.
Turner (2019) relaciona en la Tabla 2.1 qué aporta Lean y qué Seis Sigma al sistema híbrido Lean Seis Sigma:
Lean | Seis Sigma |
---|---|
Guía para la producción (sistema Pull). | Herramientas estadísticas potentes para el análisis y la mejora. |
Cultura de la mejora continua (Kaizen). | |
Eliminación incesante de los desechos. | Foco en la reducción de la variación y defectos. |
Enfoque esencial en crear valor para el cliente. | Gran peso de la Voz del Cliente (VOC) para determinar sus necesidades. |
2.4 Principios Lean Seis Sigma
Turner (2019) resume de forma muy precisa las características básicas de la metodología Lean Seis Sigma, compendiando las que ya hemos presentado para Lean y Seis Sigma de forma separada:
- Priorizar las necesidades de los clientes. Se invierte en aquello que mejorará la percepción de calidad del cliente, pues es el que comprará los productos si le convencen.
- Introducir fluidez en los procesos, identificando y eliminando los cuellos de botella.
- Añadir valor a través de reducir desechos, sabiendo de antemano que los desechos más habituales son los vinculados a la sobreproducción, demoras en los tiempos, costes logísticos y de transporte, manejo de stocks, defectos, basura en el proceso y relacionados con la movilidad. Al hacer visibles los desechos, se toman medidas específicas para reducirlos o eliminarlos, y así dar valor a cada uno de los procesos que contribuyen al resultado o producto que llega al cliente.
- Eliminar variación. Porque la variabilidad introduce basura/desechos y defectos. La estandarización de procesos contribuirá notablemente a la reducción de la variación.
- Colaborar. Para que las decisiones que se toman en la organización sean efectivas, es preciso incluir a todos los agentes, desde la dirección hasta los empleados, implicándolos como protagonistas de los logros de mejora.
- Hacer esfuerzos científicos y sistemáticos. Utilizar los datos para la toma de decisiones y la sistematización y control de mejoras.
- Comprender los procesos (process mining), para identificar los que no funcionan, mejorarlos y chequear su funcionamiento una vez mejorados, mediante software y herramientas analíticas específicas.
2.5 Leyes Lean Seis Sigma
Para mejorar la velocidad de los procesos y reducir simultáneamente los defectos, hay que identificar y eliminar las fuentes de retrasos mediante las Tres Leyes de Lean Seis Sigma, que siguen a una ley cero o ley del mercado, y que son:
- LEY CERO: La Ley del Mercado. Las cuestiones que resultan críticas para la calidad al cliente son las que han de ser tratadas en primer lugar.
- PRIMERA LEY: La Ley de la Flexibilidad. La velocidad de un proceso es directamente proporcional a la flexibilidad. En un proceso de manufactura, la flexibilidad es proporcional a la rotación de las estaciones de trabajo. Se consigue la máxima flexibilidad cuando el tamaño de los lotes se minimiza según: Mínimo tamaño lotes = (ratio de demanda por clientes) x (tiempo de rotación de las estaciones de trabajo)
- SEGUNDA LEY: La Ley del Foco. El 80% del retraso en cualquier proceso es provocado por el 20% de las actividades.
- TERCERA LEY: La Ley de la Velocidad. La velocidad media del flujo de un proceso es inversamente proporcional al número de “cosas” en curso o trabajo en proceso (WIP, Work in Progress) y a la variación promedio entre la oferta y la demanda.
2.6 Implementación
Muy brevemente, el desarrollo de un proyecto de mejora Lean Seis Sigma se estructura, según George (2002), en las siguientes fases o etapas:
- Iniciación.
- Diseñar de modo detallado el despliegue de la estrategia Lean Seis Sigma, y concretar la infraestructura necesaria y planificación.
- Ilustrar al equipo directivo/CEO sobre los beneficios del Lean Seis Sigma. Conseguir su implicación y aprobación del proyecto, ante unos objetivos financieros y de mejora, para un horizonte de 2 a 5 años.
- Selección de proyectos y recursos.
- Seleccionar a Champions y BlackBelts de entre líderes potenciales en la organización, para liderar el proyecto.
- Implicar a los champion en la mejora de procesos vitales y la selección de proyectos con más valor para el cliente, alineando los requisitos de estos con los objetivos de la empresa.
- Entrenar a los BlackBelts, tanto en estrategias de liderazgo como en herramientas Lean Seis Sigma.
- Implementación, sostenibilidad, evolución.
- Proporcionar asesoramiento de expertos en los proyectos iniciales.
- Trazar el seguimiento de los proyectos a través del proceso DMAIC hasta los resultados finales.
- Introducir e implementar Lean Seis Sigma en todos los procesos de la organización, y generar la capacidad de que Lean Seis Sigma perdure como la herramienta base de desarrollo y mejora continua de la empresa.
Serán preguntas clave para la implementación:
- ¿Dónde enfocar? Cómo y con qué herramientas seleccionar los proyectos de mayor valor para los clientes.
- ¿Cómo ejecutar el cambio? A través de un proceso DMAIC en combinación con otras herramientas Lean.
- ¿Quién va a liderar el cambio? Pues la visión y trabajo de los líderes que desarrollen el proyecto será clave para conseguir un cambio real, efectivo y de un modo eficiente.
La implementación de un proyecto Lean Seis Sigma no siempre resulta exitosa, pues requiere de un esfuerzo importante en muchos frentes. Según la propuesta de George (2002), la implementación de un proyecto Seis Sigma (ver Figura 2.1) se organiza en las siguientes fases:
- Diseño detallado de la infraestructura y el modo en que se va a llevar a cabo el proyecto.
- Conseguir el compromiso del resto de líderes de la organización. Lanzamiento del proyecto a nivel ejecutivo.
- Los líderes y gestores de la organización seleccionan a los champions y Black Belts, que liderarán la implementación.
- Los champions conectan las unidades estratégicas del negocio con las necesidades dentro del programa de mejora, a través de la selección de procesos del proyecto.
- Entrenamiento de los champions y black belts, durante un periodo aproximado de 4 a 6 meses, en las que asisten a sesiones formativas durante una semana al mes y empiezan en simultáneo a trabajar en los proyectos.
- Durante esta etapa de inicio y entrenamiento, los líderes participan en reuniones de equipo, revisiones iniciales y seguimiento de la comunicación.
- El despliegue del proyecto debería estar organizado para incrementar progresivamente los beneficios con el avance del proyecto, y visibilizarlos.
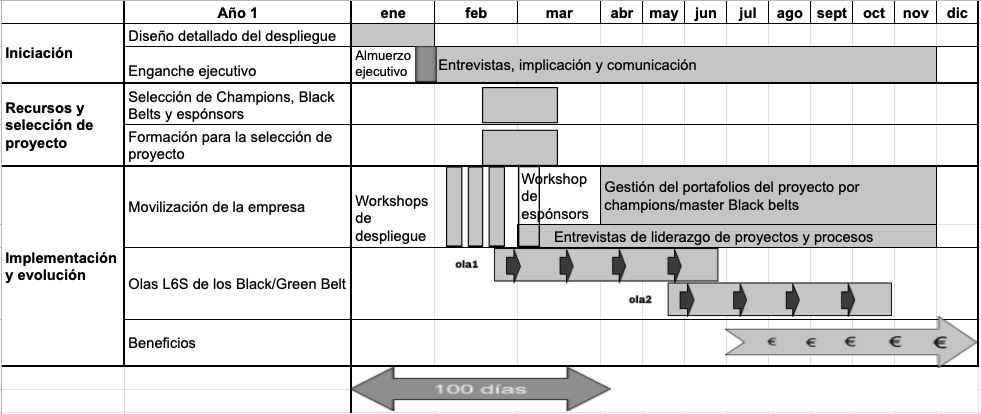
Figura 2.1: Línea temporal en la implementación de un proyecto Lean Seis Sigma. Traducido de George (2002).
El libro de George et al. (2002) proporciona un manual rápido con las herramientas y funcionalidades a emplear en un proyecto Lean Seis Sigma.
2.7 Impulso y aceleración
Una vez está implementado un proyecto de mejora Seis Sigma, Lean completa el esfuerzo para lograr un aumento de las velocidades de producción, una adaptación a la demanda en tiempos breves, una reducción de las necesidades de almacenaje e inventario, y la incorporación de un sistema de producción Pull en el que se produce a medida de la demanda, abaratando considerablemente los costes globales.
Unos tiempos de producción/servicio altos en los procesos provocan, según George (2002), una serie de desventajas a las empresas:
- generan mucha variación en dichos tiempos,
- provocan costes adicionales por horas extras, desperdicios y retrabajo,
- originan costes ocultos vinculados a sobredimensionamiento de espacios y personal,
- generan un acúmulo de productos manufacturados que, al permanecer almacenados pueden originar, además de los costes base de almacenamiento, costes de calidad, obsolescencia y bajos márgenes de venta.
Todos estos sobrecostes son un motivo para que la empresa reduzca tanto los tiempos de producción, como su variación. La cuestión sobre cómo conseguir estas reducciones se responde con:
La Tercera ley de Lean Seis Sigma: la velocidad del proceso y de la producción dependen del número de “objetos en proceso” (WIP, Work in Progress), por lo que reducir el WIP permite acelerar el proceso.
La aceleración de la cadena de suministro, que nos dice que el proceso en sí mismo dicta cuál es la mínima cantidad de inventario WIP requerido para una demanda dada.
En consecuencia, será preciso:
- especificar un máximo en la cantidad de WIP para tener capacidad de predecir el tiempo de producción,
- adaptar el WIP a la demanda actual, para mantener un flujo/velocidad constante en la cadena de producción,
- para prevenir un exceso de WIP, liberar material en las líneas de producción, consistente con el tamaño mínimo de los lotes de procesado.
El software de aceleración de la cadena de suministro permitirá calcular el mínimo tamaño de lote preciso para: a) compensar la estación de trabajo que genera tiempos de retraso mayores, y b) proporcionar en la línea de producción la cantidad justa de material necesario para mantener el mínimo WIP y el tiempo de producción global más rápido.
George (2002) remarca que el eje principal de un sistema de producción hacia la demanda que minimiza el WIP es el sistema Pull en conjunción con el sistema Kanban. El sistema de producción Pull ya lo definimos previamente; Kanban es un sistema de información que controla de modo armónico la fabricación de los productos necesarios en la cantidad y tiempo necesarios, en cada uno de los procesos que tienen lugar en la empresa o entre las fábricas que se relacionan para la producción (Wikipedia n.d.). Integrados ambos sistemas, cada proceso retira del proceso anterior sólo las cantidades de elementos que se han usado, teniendo en cuenta que:
- Es necesario guardar cierta cantidad de productos a mano para abastecer a los clientes. Esta reserva se denomina “reserva estratégica” (strategic buffer).
- Cuando un item es extraído de la reserva, se desencadena una alerta, física o electrónica, que alerta a la parte inicial del sistema de producción de que la reserva está baja (originariamente se utilizaban tarjetas para anotar estas alertas, y de ahí el término Kanban, que significa “tarjeta” en japonés).
- El sistema de producción produce entonces un item para rellenar la reserva.
El sistema Pull es especialmente exitoso para procesos de producción repetitivos (como cadenas de montaje), donde la desviación estándar de la demanda no es superior al 30% de la demanda media. Cuando los procesos no son repetitivos, los sistemas Pull utilizan niveles de inventario para conducir los pedidos.
En cualquier caso, una dinámica Pull afecta a todos los niveles del sistema de producción: una estación de trabajo produce sólo lo suficiente para rellenar lo que la siguiente estación va a utilizar; un proceso rellena lo que el siguiente proceso está usando; una fábrica produce sólo lo que el distribuidor o cliente solicita.
Para calcular la dimensión de la reserva estratégica, que funciona como el tope de la cantidad de inventario WIP, hay que considerar cinco aspectos:
- La reserva temporal de producción (RTP). Siempre será preciso tener suficiente inventario para atender la demanda durante el tiempo que tarda la fábrica en producir una nueva orden. Este tiempo se calcula con el producto del tiempo de producción (en días) de cada unidad (manufacturing lead time, MLT) por la demanda promedio de unidades por día (Demanda). \[RTP=MLT \ \times \ Demanda.\]
- La reserva temporal de ciclo (RTC). Si una fábrica fabrica en ciclos un Producto1, luego un Producto2, etc, hasta volver a fabricar el Producto1 habrá de tener suficiente inventario para atender la demanda. El tiempo que transcurre entre los ciclos de producción de un mismo producto es el intervalo temporal de ciclo (cycle time interval, CTI). La reserva temporal de ciclo se calculará con el CTI multiplicado por la demanda promedio por día. \[RTC=CTI \ \times \ Demanda.\]
- La reserva temporal de transporte (RTT). Cuando hay distancia geográfica entre el suministro y la demanda, es preciso considerar el tiempo de transporte en días (TT) de la demanda promedio por día (Demanda). \[RTT=TT \ \times \ Demanda.\]
- Stock de seguridad (SS). Cada uno de los anteriores procesos tiene un valor promedio sujeto a fluctuación e incertidumbre. También ocurre así con la demanda. La fórmula del stock de seguridad ha de considerar ambas fuentes de fluctuación.
- Estacionalidad o promociones (E). Es preciso considerar también las necesidades de inventario utilizando históricos y predicciones, pero siempre incorporando los consumos actuales.
Todas estas reservas se pueden obtener empíricamente y se pueden confirmar con un análisis con hoja de cálculo, o modelados con software acelerador de cadena de suministros. También se puede calcular la cantidad de reserva estratégica, utilizando la siguiente ecuación:
Máxima reserva estratégica = RTP + RTC + RTT + SS + E.
Si el volumen de inventario en la reserva cae a un nivel igual a ‘RTP + SS,’ entonces hay un inventario justo, suficiente para mantener a los clientes satisfechos hasta que llegue un nuevo lote de materiales, pero motivo de alarma. Si la reserva cae por debajo del ‘SS,’ entonces la alarma es crítica.
Cuando se establece un sistema Pull, se puede atacar el tiempo de producción utilizando una reducción de instalaciones, del tamaño de los lotes, etc., en las estaciones de trabajo que contribuyen más al volumen de negocios.
2.8 Conclusiones
En este capítulo hemos tratado de exponer de un modo liviano pero no sesgado los distintas conceptos y consideraciones que definen un proyecto Lean Seis Sigma. A partir de ahora, en este manual, nos dedicaremos a la parte más estadística de un proyecto Lean Seis Sigma y que tiene que ver más con la aplicación de la metodología Seis Sigma: la implementación de la dinámica DMAIC para trabajar hacia la mejora de un modo objetivo y fundamentado en datos. Algunas de las técnicas que veremos también se consideran técnicas Lean, pero no entraremos en la mayoría de las técnicas Lean que se presentaron en la Sección 1.4.5, especialmente en las más sofisticadas. Al final del Capítulo 8 damos recomendaciones al lector interesado, para completar su formación en Lean.